Polydodecalactam and multistage-series polymerization method for polydodecalactam modified resin
A technology of polylaurolactam and laurolactam, which is applied in the field of polyamide materials, can solve the problems of unfavorable polycondensation molecular weight, poor flexibility, short residence time, etc., so as to avoid unfavorable polycondensation process and molecular weight growth, and ensure stability and stability. Reliability, resistance to bumping and clogging
- Summary
- Abstract
- Description
- Claims
- Application Information
AI Technical Summary
Problems solved by technology
Method used
Image
Examples
Embodiment 1
[0067] The preparation of PA12 pure resin products adopts a 5-stage series polymerization process
[0068] 500kg of molten monomer laurolactam and 75kg of water are input into the reactor R1 (anchor stirring) from the raw material inlet, and 1kg of terephthalic acid is added from the feed inlet A1 as a molecular weight stabilizer, and the working temperature of the kettle is maintained at 300°C. Airtight reaction, the pressure (gauge pressure) is 5.0MPa, and the residence time is 1h; then the valve V1 is opened, and the material is transported to R2 (anchor stirring), where the pressure (gauge pressure) in the kettle is stabilized at 3MPa, the reaction temperature is 290°C, and the residence time is 1h. The material is further prepolymerized here, and the monomer conversion rate is increased to 99.95% (that is, the residual order is 0.05%); then the valve V3 is opened, and the material is transported to R3 (screw Belt stirring), where the pressure (gauge pressure) in the kettl...
Embodiment 2
[0070] The preparation of PA12 additive compound products adopts a 5-stage series polymerization process
[0071] 500kg of molten monomer laurolactam and 25kg of water are input into the reactor R1 (anchor stirring) from the raw material port, and 4kg of dodecanedioic acid is added from the feeding port A1 as a molecular weight stabilizer, and the working temperature of the kettle is maintained at 280°C , airtight reaction, the pressure (gauge pressure) range is 4.0MPa, and the residence time is 3h; then the valve V1 is opened, the material is transported to R2 (anchor stirring), and 0.75kg IRGANOX 1098 and 0.75kg IRGAFOS 168 are added from A2 as antioxidant agent, the pressure (gauge pressure) in the kettle is stabilized at 1MPa through the pressure regulating valve V2, the reaction temperature is 270°C, and the residence time is 3h. The material is further prepolymerized here, and the monomer conversion rate is raised to 99.92% (ie Residual list is 0.08%); Then open valve V3...
Embodiment 3
[0073] Preparation of PA6 / 66 / 12 copolymer resin, using 5-stage series polymerization process
[0074]200kg of molten monomer laurolactam and 30kg of water are input into the reactor R1 (anchor stirring) from the raw material port, and 100kg of caprolactam is added from the feed port A1 as a comonomer, and 2kg of hexamethylenediamine is added as a molecular weight stabilizer. Keep the working temperature of 290°C, seal the reaction, the pressure (gauge pressure) is 4.5MPa, and the residence time is 2h; then open the valve V1, transfer the material to R2 (anchor stirring), and add 0.8kg IRGANOX245 and 0.8kg IRGAFOS126 from A2 as Antioxidant, add the 60% aqueous solution that 200kg nylon 66 salt prepares as comonomer, the pressure (gauge pressure) in the kettle is stabilized at 2MPa by pressure regulating valve V2, and reaction temperature is 280 ℃, and residence time is 2h, and material Further pre-polymerization and copolymerization here, the monomer conversion rate is brought ...
PUM
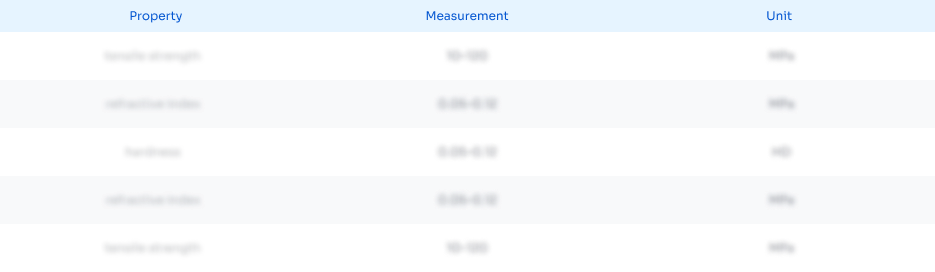
Abstract
Description
Claims
Application Information

- R&D Engineer
- R&D Manager
- IP Professional
- Industry Leading Data Capabilities
- Powerful AI technology
- Patent DNA Extraction
Browse by: Latest US Patents, China's latest patents, Technical Efficacy Thesaurus, Application Domain, Technology Topic, Popular Technical Reports.
© 2024 PatSnap. All rights reserved.Legal|Privacy policy|Modern Slavery Act Transparency Statement|Sitemap|About US| Contact US: help@patsnap.com