Method for producing dimethyl carbonate by urea alcoholysis method
A technology of dimethyl carbonate and urea alcohol, which is applied in the preparation of carbonate/haloformate, chemical instruments and methods, and the preparation of urea derivatives, etc. It can solve the problem of difficult precise control of propylene glycol stripping time and rapid price changes , Reduce the yield of propylene glycol and other issues, achieve the effect of improving the conversion rate of urea and product yield, reducing the generation of by-products, and solving the high cost of raw materials
- Summary
- Abstract
- Description
- Claims
- Application Information
AI Technical Summary
Problems solved by technology
Method used
Image
Examples
Embodiment 1
[0029] Embodiment 1 utilizes the method of urea alcoholysis to produce dimethyl carbonate
[0030] Proceed as follows:
[0031] (1) Preparation of urea with carbon dioxide and liquid ammonia as raw materials: inject preheated carbon dioxide and liquid ammonia (preheated to 40°C) into the urea synthesis tower with a pump, and react for 0.5 hours at 140°C and 13 MPa pressure ; The urine synthesized from the urea synthesis tower is decomposed, recovered, and evaporated under reduced pressure to obtain molten urea liquid for subsequent use.
[0032](2) Using urea (the molten urea prepared above) and methanol as raw materials (the molar ratio of methanol to urea is 2.5:1), in an alkaline composite liquid catalyst (composed of methanol solution of methylamine and sodium methylate, formaldehyde Amine accounts for 35%, and sodium methylate accounts for 15%, and methyl alcohol accounts for 50%. The consumption of alkaline composite liquid catalyst is 5% of methanol weight) direct reac...
Embodiment 2
[0034] Embodiment 2 utilizes the method of urea alcoholysis to produce dimethyl carbonate
[0035] Proceed as follows:
[0036] (1) Preparation of urea with carbon dioxide and liquid ammonia as raw materials: inject preheated carbon dioxide and liquid ammonia (preheated to 40°C) into the urea synthesis tower with a pump, and react for 0.5 hours at 140°C and 13 MPa pressure ; The urine synthesized from the urea synthesis tower is decomposed, recovered, and evaporated under reduced pressure to obtain molten urea liquid for subsequent use.
[0037] (2) Using urea (the molten urea prepared above) and methanol as raw materials (the molar ratio of methanol to urea is 2.5:1), in an alkaline composite liquid catalyst (composed of methanol solution of methylamine and sodium methylate, formaldehyde Amine accounts for 30%, sodium methoxide accounts for 20%, and methyl alcohol accounts for 50%. The consumption of alkaline composite liquid catalyst is 6% of methanol weight) direct reactio...
Embodiment 3
[0039] Embodiment 3 utilizes the method for urea alcoholysis to produce dimethyl carbonate
[0040] Proceed as follows:
[0041] (1) Preparation of urea with carbon dioxide and liquid ammonia as raw materials: inject preheated carbon dioxide and liquid ammonia (preheated to 40°C) into the urea synthesis tower with a pump, and react for 0.5 hours at 140°C and 13 MPa pressure ; The urine synthesized from the urea synthesis tower is decomposed, recovered, and evaporated under reduced pressure to obtain molten urea liquid for subsequent use.
[0042] (2) With urea (the molten urea prepared above) and methanol as raw materials (the molar ratio of methanol to urea is 3:1), in an alkaline composite liquid catalyst (composed of methanol solution of methylamine and sodium methylate, formaldehyde Amine accounts for 25%, and sodium methylate accounts for 25%, and sodium methylate accounts for 50%. The consumption of alkaline composite liquid catalyst is 8% of methanol weight) direct rea...
PUM
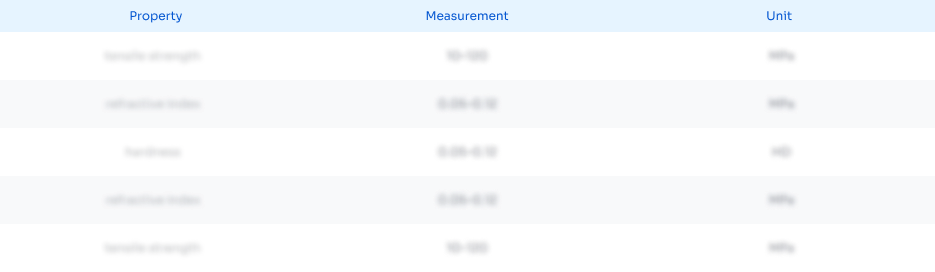
Abstract
Description
Claims
Application Information

- R&D
- Intellectual Property
- Life Sciences
- Materials
- Tech Scout
- Unparalleled Data Quality
- Higher Quality Content
- 60% Fewer Hallucinations
Browse by: Latest US Patents, China's latest patents, Technical Efficacy Thesaurus, Application Domain, Technology Topic, Popular Technical Reports.
© 2025 PatSnap. All rights reserved.Legal|Privacy policy|Modern Slavery Act Transparency Statement|Sitemap|About US| Contact US: help@patsnap.com