Low-temperature polycrystalline silicon film, preparation method thereof, thin film transistor and display panel
A low-temperature polysilicon and thin-film technology, applied in the direction of transistors, electric solid-state devices, semiconductor devices, etc., can solve the problems of reducing the electrical performance of thin-film transistors, increasing the leakage current of thin-film transistors, and the instability of threshold voltage of thin-film transistors. Current, the effect of improving electrical performance
- Summary
- Abstract
- Description
- Claims
- Application Information
AI Technical Summary
Problems solved by technology
Method used
Image
Examples
Embodiment 1
[0034] Such as figure 1 As shown, the preparation method of the low-temperature polysilicon thin film of embodiment one of the present invention comprises:
[0035] Step 101, depositing multiple layers of amorphous silicon layers with different film quality parameters; wherein the film quality parameters include refractive index parameters and / or thermal conductivity parameters;
[0036] Step 102, performing dehydrogenation treatment on the multi-layer amorphous silicon layers with different film quality parameters;
[0037] Step 103, performing crystallization treatment on the dehydrogenated amorphous silicon layer to form a low-temperature polysilicon film.
[0038] In the embodiment of the present invention, by depositing multiple layers of amorphous silicon layers with different film quality parameters, the refractive index and thermal conductivity of amorphous silicon with different film quality parameters are different, which is conducive to forming a uniform 400-500nm ...
Embodiment 2
[0058] Such as image 3 and Figure 4 As shown, this embodiment takes depositing four layers of amorphous silicon layers as an example, including the following steps:
[0059] 301, depositing the first layer of amorphous silicon layer
[0060] In this step, the first layer of amorphous silicon layer 211 (also called amorphous silicon film) is deposited on the buffer layer 20. The deposition temperature of this layer of amorphous silicon layer is the lowest, and the gas flow ratio is the smallest (SiH 4 / H 2 ), under this condition, the formed amorphous silicon layer has a small refractive index, a small thermal conductivity, and a relatively loose film quality.
[0061] 302, depositing a second amorphous silicon layer
[0062] This step is to change the PECVD process parameters after step 301 is completed, continue to deposit the second layer of amorphous silicon layer 212 on the surface of the first layer of amorphous silicon, the layer deposition temperature increases, a...
application example 1
[0072] Deposit 50nm and 300nm SiN on glass substrates using PECVD process x and SiO 2 Form SiN x and SiO 2 Double buffer layer. Use PECVD process to deposit nano-silicon thin film layer on the double buffer layer, the reaction gas is silane (SiH 4 ) and hydrogen (H 2 ), wherein, the first layer of amorphous silicon deposition parameters, the gas flow of silane is 140sccm, the gas flow of hydrogen is 1200sccm, the radio frequency power is 120W; the working pressure is 290Pa; the temperature is 370°C; the deposition time is 20 seconds. Then change the PECVD parameters to carry out the second layer of amorphous silicon deposition, the second layer of amorphous silicon deposition parameters, the gas flow of silane is 160sccm, the gas flow of hydrogen is 1200sccm, the radio frequency power is 120W; the working pressure is 290Pa, the temperature is 390°C, The deposition time was 20 seconds. Continue to change the PECVD parameters to carry out the third layer of amorphous silic...
PUM
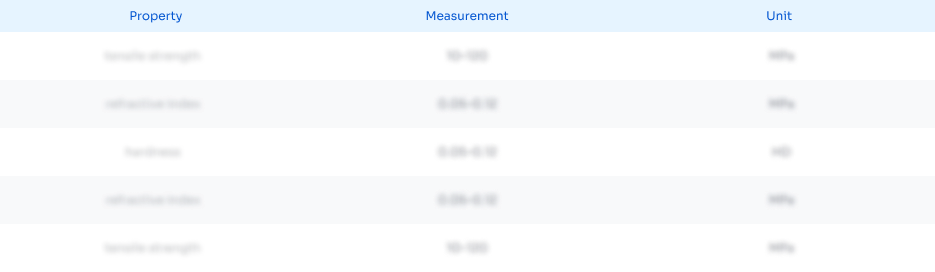
Abstract
Description
Claims
Application Information

- R&D
- Intellectual Property
- Life Sciences
- Materials
- Tech Scout
- Unparalleled Data Quality
- Higher Quality Content
- 60% Fewer Hallucinations
Browse by: Latest US Patents, China's latest patents, Technical Efficacy Thesaurus, Application Domain, Technology Topic, Popular Technical Reports.
© 2025 PatSnap. All rights reserved.Legal|Privacy policy|Modern Slavery Act Transparency Statement|Sitemap|About US| Contact US: help@patsnap.com