Preparation method for porous Au coating inhibiting microdischarge effect
A micro-discharge effect and coating technology, applied in coating, metal material coating process, liquid chemical plating, etc., can solve the problem of damaged surface performance, poor environmental stability of trap structure silver, complex ion beam etching process, etc. problem, to achieve the effect of good environmental stability
- Summary
- Abstract
- Description
- Claims
- Application Information
AI Technical Summary
Problems solved by technology
Method used
Image
Examples
Embodiment 1
[0034] (1) Use 50mL HF / HNO 3 / H 2 The O etching system etched the silver-coated aluminum alloy with a length of 20 mm, a width of 12 mm, and a height of 1 mm. The etching temperature was 25 °C and the etching time was 2 min. The silver-coated aluminum alloy was cleaned with 50 mL of deionized water and then Sonicate for 3 minutes, and dry in a 50°C oven for 30 minutes. Then, 12g of Fe(NO 3 ) 3 The sample was etched with an aqueous solution, the etching temperature was 45°C, and the etching time was 35s. The silver-plated aluminum alloy was cleaned with 50mL deionized water and ultrasonicated for 3 minutes, and dried in an oven at 50°C for 30 minutes. Among them, HF / HNO 3 / H 2 The O etching system is prepared by the following method: mix hydrofluoric acid, nitric acid and water uniformly to obtain HF / HNO 3 / H 2 O etching system, wherein the volume ratio of hydrofluoric acid, nitric acid and water in every 50mL is 2:12.5:35.5.
[0035] (2) Immerse the silver-plated alumi...
Embodiment 2
[0038] (1) Use 50mL HF / HNO 3 / H 2The O etching system etched the silver-coated aluminum alloy with a length of 20 mm, a width of 12 mm, and a height of 1 mm. The etching temperature was 30 °C and the etching time was 4 min. The silver-coated aluminum alloy was cleaned with 100 mL of deionized water and removed. Sonicate for 3 minutes, and dry in an oven at 70°C for 40 minutes. Then, 12g of Fe(NO 3 ) 3 The sample was etched with an aqueous solution, the etching temperature was 55°C, and the etching time was 45s. The silver-plated aluminum alloy was cleaned with 100mL deionized water and ultrasonicated for 3 minutes, and dried in an oven at 70°C for 40 minutes. Among them, HF / HNO 3 / H 2 The O etching system is prepared by the following method: mix hydrofluoric acid, nitric acid and water uniformly to obtain HF / HNO 3 / H 2 O etching system, wherein the volume ratio of hydrofluoric acid, nitric acid and water in every 50mL is 3.5:12.5:34.
[0039] (2) Immerse the silver-pla...
Embodiment 3
[0042] (1) Use 50mL HF / HNO 3 / H 2 The O etching system etches the silver-coated aluminum alloy with a length of 20 mm, a width of 12 mm, and a height of 1 mm. The etching temperature is 28 °C, and the etching time is 3 min. The silver-coated aluminum alloy is cleaned with 100 mL of deionized water and removed Sonicate for 3 minutes, and dry in an oven at 60°C for 40 minutes. Then, 12g of Fe(NO 3 ) 3 The sample was etched with an aqueous solution, the etching temperature was 50°C, and the etching time was 40s. The silver-plated aluminum alloy was cleaned with 100mL deionized water, ultrasonicated for 3min, and dried in an oven at 60°C for 40min. Among them, HF / HNO 3 / H 2 The O etching system is prepared by the following method: mix hydrofluoric acid, nitric acid and water uniformly to obtain HF / HNO 3 / H 2 O etching system, wherein the volume ratio of hydrofluoric acid, nitric acid and water in every 50mL is 3:12.5:34.5.
[0043] (2) Immerse the silver-plated aluminum al...
PUM
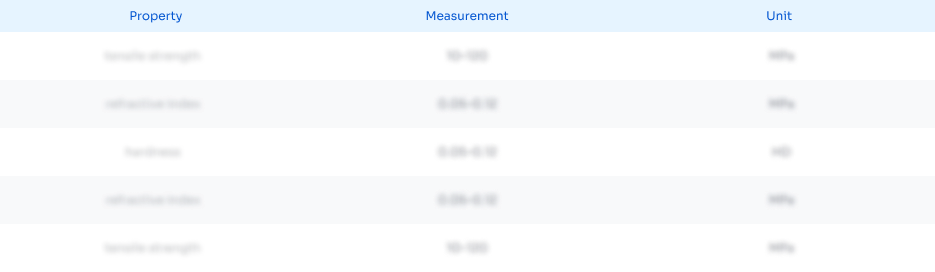
Abstract
Description
Claims
Application Information

- R&D
- Intellectual Property
- Life Sciences
- Materials
- Tech Scout
- Unparalleled Data Quality
- Higher Quality Content
- 60% Fewer Hallucinations
Browse by: Latest US Patents, China's latest patents, Technical Efficacy Thesaurus, Application Domain, Technology Topic, Popular Technical Reports.
© 2025 PatSnap. All rights reserved.Legal|Privacy policy|Modern Slavery Act Transparency Statement|Sitemap|About US| Contact US: help@patsnap.com