Composite stepped carburizing and quenching technology of gear shaft
A carburizing and quenching, gear shaft technology, applied in the field of heat treatment, can solve the problems of not meeting the ideal requirements, high wear resistance, hardness and fatigue strength requirements, etc., to reduce heat treatment deformation, increase diffusion speed, and reduce heating speed Effect
- Summary
- Abstract
- Description
- Claims
- Application Information
AI Technical Summary
Problems solved by technology
Method used
Image
Examples
Embodiment 1
[0032] The same batch of gear shafts in Table 1 were heat treated by the conventional carburizing and quenching process and the above-mentioned compound step carburizing and quenching process respectively. The comparison results are shown in the following table. Table 2 is the conventional process, and Table 3 is the compound step carburizing and quenching process:
[0033]
[0034] Table 2: Conventional carburizing and quenching process
[0035]
[0036] Table 3: Composite step carburizing and quenching process
Embodiment 2
[0038] The same batch of gear shafts in Table 1 were heat treated by the conventional carburizing and quenching process and the above-mentioned compound step carburizing and quenching process respectively. The comparison results are shown in the following table. Table 4 is the conventional process, and Table 5 is the compound step carburizing and quenching process
[0039]
[0040] Table 4: Conventional carburizing and quenching process
[0041]
[0042] Table 5: Composite step carburizing and quenching process
[0043] According to the data comparison of the same batch of gear shafts before heat treatment in Example 1 and Example 2 after heat treatment by conventional carburizing process and composite step carburizing process, it can be seen that after heat treatment by conventional carburizing process, the helical error of the gear is relatively small. Large, the precision of the helix is greatly reduced, and after heat treatment using the composite step carburizing ...
PUM
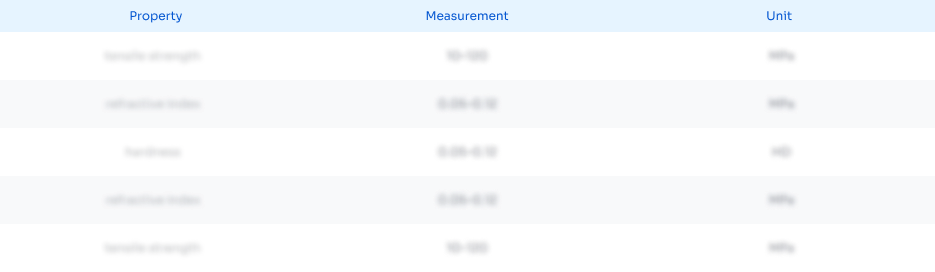
Abstract
Description
Claims
Application Information

- R&D
- Intellectual Property
- Life Sciences
- Materials
- Tech Scout
- Unparalleled Data Quality
- Higher Quality Content
- 60% Fewer Hallucinations
Browse by: Latest US Patents, China's latest patents, Technical Efficacy Thesaurus, Application Domain, Technology Topic, Popular Technical Reports.
© 2025 PatSnap. All rights reserved.Legal|Privacy policy|Modern Slavery Act Transparency Statement|Sitemap|About US| Contact US: help@patsnap.com