Environment-friendly silver metal oxide rivet touch head producing method
An oxide, environmentally friendly technology, applied in the direction of nails, furnace types, mechanical equipment, etc., can solve the problem of cracks easily caused by rivets, and achieve the effect of overcoming low processing plasticity, reducing deformation, and simple process control
- Summary
- Abstract
- Description
- Claims
- Application Information
AI Technical Summary
Problems solved by technology
Method used
Examples
Embodiment 1
[0007] Embodiment 1: Put the silver tin oxide wire material with a diameter of φ2.38mm into a cold heading riveting machine, adjust the appropriate cold heading speed to pre-upset it into a pre-upsetting ball with a diameter of φ3.9mm. The pre-headed balls were annealed at 900°C for 1 hour. Then it was cleaned and dried at 300°C for 1 hour. Put the cleaned and dried pre-upsetting balls into the vibrating plate of the rotary rivet stamping machine, adjust the stamping speed to 50 grains / minute, so that the pre-upsetting balls are stamped and formed at the stamping station of the rotary rivet stamping machine φ5.0mm rivet contact, and then anneal the rivet at 900°C for 1 hour to obtain a soft crack-free finished rivet.
Embodiment 2
[0008] Embodiment 2: Put the silver tin oxide wire material with a diameter of φ2.38mm into a cold heading riveting machine, adjust the appropriate cold heading speed to pre-upset it into a pre-upsetting ball with a diameter of φ3.9mm. The pre-headed balls were annealed at 150°C for 8 hours. Then it was cleaned and dried at 110°C for 6 hours. Put the cleaned and dried pre-upsetting balls into the vibrating plate of the rotary rivet stamping machine, adjust the punching speed to 30 grains / minute, so that the pre-upsetting balls are stamped and formed at the stamping station of the rotary rivet stamping machine φ5.0mm rivet contact, and then anneal the rivet at 150°C for 8 hours to obtain a soft crack-free finished rivet.
Embodiment 3
[0009] Embodiment 3: put the silver tin oxide wire material with a diameter of φ2.38mm into a cold heading riveting machine, adjust the appropriate cold heading speed to pre-upset it into a pre-upsetting ball with a diameter of φ3.9mm. The pre-headed balls were annealed at 525°C for 4.5 hours. It was then cleaned and dried at 205°C for 3.5 hours. Put the cleaned and dried pre-upsetting balls into the vibrating plate of the rotary rivet stamping machine, adjust the stamping speed to 40 grains / minute, so that the pre-upsetting balls are stamped and formed at the stamping station of the rotary rivet stamping machine φ5.0mm rivet contact, and then anneal the rivet at 525°C for 4.5 hours to obtain a soft crack-free finished rivet.
PUM
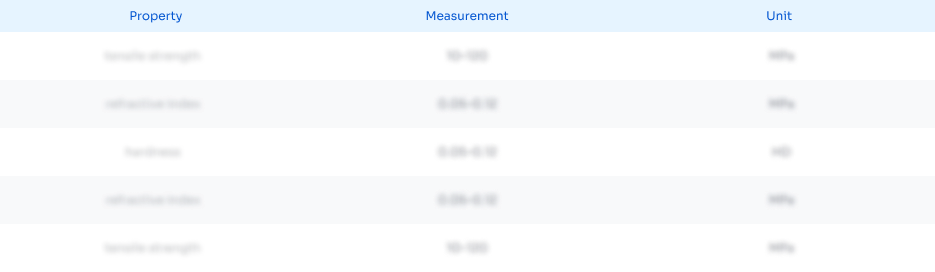
Abstract
Description
Claims
Application Information

- R&D
- Intellectual Property
- Life Sciences
- Materials
- Tech Scout
- Unparalleled Data Quality
- Higher Quality Content
- 60% Fewer Hallucinations
Browse by: Latest US Patents, China's latest patents, Technical Efficacy Thesaurus, Application Domain, Technology Topic, Popular Technical Reports.
© 2025 PatSnap. All rights reserved.Legal|Privacy policy|Modern Slavery Act Transparency Statement|Sitemap|About US| Contact US: help@patsnap.com