Manufacturing technique for automobile magnesium alloy gearbox bracket
A gearbox bracket and production process technology, which is applied in the field of production technology of magnesium alloy gearbox brackets for automobiles, can solve the problems of poor deformation ability, limited development, high cost, etc., and achieve increased alloy nucleation probability and good elastic deformation resistance , Improve the effect of heat resistance
- Summary
- Abstract
- Description
- Claims
- Application Information
AI Technical Summary
Problems solved by technology
Method used
Examples
Embodiment 1
[0019] A production process for a magnesium alloy transmission bracket for automobiles, comprising the steps of:
[0020] Put the aluminum ingot into the crucible A and heat it until it melts, then add copper and strontium, then raise the temperature to 1120°C, keep it warm for 30 minutes to obtain a melt; insert the ultrasonic horn into the melt obtained above for ultrasonic treatment, the ultrasonic intensity is 1.2kw / cm 2 , the ultrasonic time is 10min; the temperature is lowered to 750°C to obtain an aluminum-copper-strontium master alloy body; the mass ratio of the aluminum ingot, copper and strontium is 100:5:2;
[0021] Preheat crucible B to 300°C, then add magnesium ingots, raise the temperature to 750°C at a rate of 10°C / S to obtain a magnesium melt, add aluminum-copper-strontium that accounts for one-tenth of the weight of the magnesium melt to the magnesium melt The intermediate alloy body is fully stirred for 15 minutes, then a modifier accounting for 1% of the we...
Embodiment 2
[0024] A production process for a magnesium alloy transmission bracket for automobiles, comprising the steps of:
[0025] Put the aluminum ingot into the crucible A and heat it until it melts, then add copper and strontium, then raise the temperature to 1120°C, keep it warm for 30 minutes to obtain a melt; insert the ultrasonic horn into the melt obtained above for ultrasonic treatment, the ultrasonic intensity is 1.2kw / cm 2 , the ultrasonic time is 10min; the temperature is lowered to 750° C. to obtain an aluminum-copper-strontium master alloy body; the mass ratio of the aluminum ingot, copper and strontium is 200:7:3;
[0026] Preheat crucible B to 300°C, then add magnesium ingots, raise the temperature to 750°C at a rate of 10°C / S to obtain a magnesium melt, add aluminum-copper-strontium that accounts for one-tenth of the weight of the magnesium melt to the magnesium melt The intermediate alloy body is fully stirred for 15 minutes, then a modifier accounting for 1% of the ...
Embodiment 3
[0029] A production process for a magnesium alloy transmission bracket for automobiles, comprising the steps of:
[0030] Put the aluminum ingot into the crucible A and heat it until it melts, then add copper and strontium, then raise the temperature to 1120°C, keep it warm for 30 minutes to obtain a melt; insert the ultrasonic horn into the melt obtained above for ultrasonic treatment, the ultrasonic intensity is 1.2kw / cm 2 , the ultrasonic time is 10min; the temperature is lowered to 750° C. to obtain an aluminum-copper-strontium master alloy body; the mass ratio of the aluminum ingot, copper and strontium is 100:7:2;
[0031] Preheat crucible B to 300°C, then add magnesium ingots, raise the temperature to 750°C at a rate of 10°C / S to obtain a magnesium melt, add aluminum-copper-strontium that accounts for one-tenth of the weight of the magnesium melt to the magnesium melt The intermediate alloy body is fully stirred for 15 minutes, then a modifier accounting for 1% of the ...
PUM
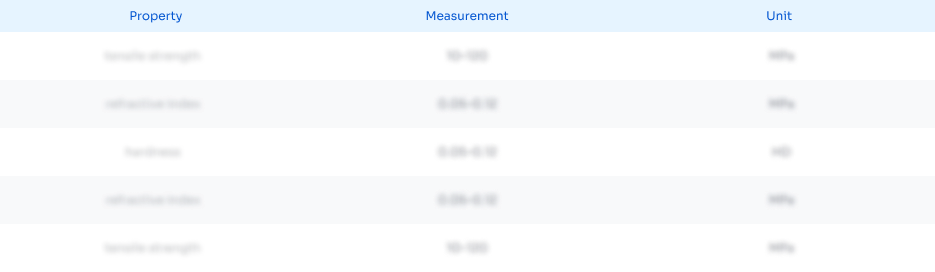
Abstract
Description
Claims
Application Information

- R&D Engineer
- R&D Manager
- IP Professional
- Industry Leading Data Capabilities
- Powerful AI technology
- Patent DNA Extraction
Browse by: Latest US Patents, China's latest patents, Technical Efficacy Thesaurus, Application Domain, Technology Topic, Popular Technical Reports.
© 2024 PatSnap. All rights reserved.Legal|Privacy policy|Modern Slavery Act Transparency Statement|Sitemap|About US| Contact US: help@patsnap.com