Method for smelting high-quality high-speed steel by pressurized electroslag remelting technology
A high-quality technology of pressurized slag, applied in the field of high-speed steel smelting, can solve the problems of increasing the cooling rate of ingots, large air gap between ingots and molds, etc. The effect of efficiency
- Summary
- Abstract
- Description
- Claims
- Application Information
AI Technical Summary
Problems solved by technology
Method used
Image
Examples
Embodiment 1
[0026] M42 high-speed steel was smelted by pressurized electroslag remelting technology, and its chemical composition is shown in Table 1. The crystallizer diameter is 200mm, the electrode diameter is 140mm, and the electrode insertion depth is 15mm.
[0027] Table 1 M42 high-speed steel chemical composition range (wt.%)
[0028]
[0029] The steps to smelt M42 high-speed steel using pressurized electroslag remelting technology are as follows:
[0030] (1) Preparation of slag
[0031] First prepare slag, the mass percentage of slag is CaF 2 : 55%, CaO: 20%, Al 2 o 3 : 20%, SiO 2 : 5%, the amount of slag is 10kg, put it into the resistance furnace after mixing, bake at 600°C for 5 hours, remove the moisture in the slag, and then turn off the power to let the slag cool down with the furnace; The bottom pad, slag and arc ignition chips of the same material are placed in the center of the bottom water tank;
[0032] (2) Molten slag
[0033] Install the upper furnace she...
Embodiment 2
[0044]M2 high-speed steel was smelted by pressurized electroslag remelting technology, and its chemical composition is shown in Table 3 below. The crystallizer diameter is 350mm, the electrode diameter is 220mm, and the electrode insertion depth is 10mm.
[0045] Table 3 M2 high-speed steel chemical composition range (wt.%)
[0046]
[0047] The steps to smelt M2 high-speed steel using pressurized electroslag remelting technology are as follows:
[0048] (1) Preparation of slag
[0049] First prepare slag, the mass percentage of slag is CaF 2 : 70%, Al 2 o 3 : 30%, the amount of slag is 30kg, put it into the resistance furnace after mixing, bake at 600°C for 5 hours, remove the moisture in the slag, and then turn off the power to let the slag cool down with the furnace; The bottom pad, slag and arc ignition chips of the same material are placed in the center of the bottom water tank;
[0050] (2) Molten slag
[0051] Install the upper furnace shell to close the furna...
Embodiment 3
[0062] The W9Mo3Cr4V high-speed steel was smelted by pressurized electroslag remelting technology, and its chemical composition is shown in Table 5 below. The crystallizer diameter is 500mm, the electrode diameter is 350mm, and the electrode insertion depth is 10mm.
[0063] Table 5 W9Mo3Cr4V high-speed steel chemical composition range (wt.%)
[0064]
[0065] The steps to smelt W9Mo3Cr4V high-speed steel using pressurized electroslag remelting technology are as follows:
[0066] (1) Preparation of slag
[0067] First prepare slag, the mass percentage of slag is CaF 2 : 40%, CaO: 30%, Al 2 o 3 : 30%, the amount of slag is 66kg, put it into the electric resistance furnace after mixing, bake at 600°C-800°C for 4-6 hours, remove the moisture in the slag material, then turn off the power to let the slag material cool down with the furnace; The bottom pad, slag and arc ignition scraps of the same material as the steel to be smelted are placed in the center of the bottom wat...
PUM
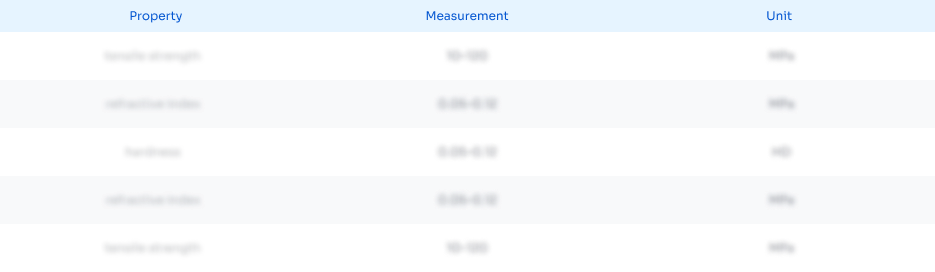
Abstract
Description
Claims
Application Information

- Generate Ideas
- Intellectual Property
- Life Sciences
- Materials
- Tech Scout
- Unparalleled Data Quality
- Higher Quality Content
- 60% Fewer Hallucinations
Browse by: Latest US Patents, China's latest patents, Technical Efficacy Thesaurus, Application Domain, Technology Topic, Popular Technical Reports.
© 2025 PatSnap. All rights reserved.Legal|Privacy policy|Modern Slavery Act Transparency Statement|Sitemap|About US| Contact US: help@patsnap.com