A gear grinding jig for high-precision quick-change shafts
A high-precision, shaft-based technology, used in gear teeth, gear cutting machines, manufacturing tools, etc., can solve the problems of high fixture cost, low repetitive motion accuracy of the manipulator, affecting processing efficiency, etc., and achieves loose parts positioning benchmark accuracy requirements, which are beneficial to The effect of automatic loading and unloading of robots and reduction of process auxiliary time
- Summary
- Abstract
- Description
- Claims
- Application Information
AI Technical Summary
Problems solved by technology
Method used
Image
Examples
Embodiment Construction
[0035] Below in conjunction with accompanying drawing, the present invention is described in further detail:
[0036] see Figure 1 to Figure 6 , a gear grinding fixture for high-precision quick-change shafts, including a connecting flange 1 connected to a machine tool, a piston 4 is arranged on the upper side of the connecting flange 1, a tie rod 6 is connected to the upper side of the piston 4, and the upper side of the tie rod 6 The side is connected with an expansion sleeve 9 through a spline, and the expansion sleeve 9 includes a number of diaphragms, and the adjacent diaphragms are bonded by elastic rubber 25, and the internal space of the piston 4 and the pull rod 6 is provided for fixing the workpiece 10. The top 11 of the center, the lower end of the top 11 is provided with an outward first annular protrusion, and the middle part of the piston 4 is provided with an inward second annular protrusion, and the first annular protrusion and the second annular protrusion coo...
PUM
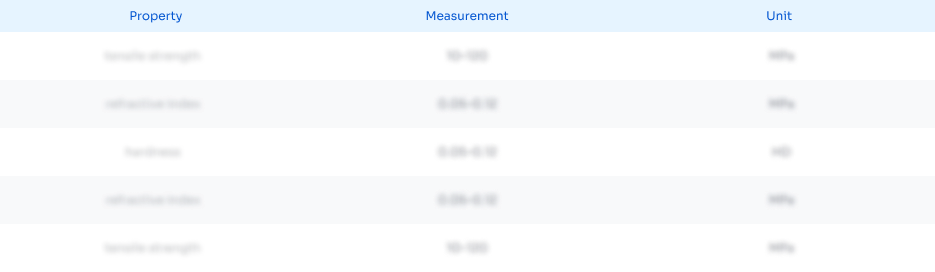
Abstract
Description
Claims
Application Information

- Generate Ideas
- Intellectual Property
- Life Sciences
- Materials
- Tech Scout
- Unparalleled Data Quality
- Higher Quality Content
- 60% Fewer Hallucinations
Browse by: Latest US Patents, China's latest patents, Technical Efficacy Thesaurus, Application Domain, Technology Topic, Popular Technical Reports.
© 2025 PatSnap. All rights reserved.Legal|Privacy policy|Modern Slavery Act Transparency Statement|Sitemap|About US| Contact US: help@patsnap.com