Method for preparing titanium dioxide pattern without residue layer by room-temperature transfer impressing technology
A technology with no residual layer and titanium dioxide, which is applied in photomechanical equipment, patterned surface photoengraving process, optics, etc., can solve the problems of limited application of TiO2, complicated process, difficult preparation, etc., and achieves low requirements for reaction equipment and mild conditions. Easy-to-control, easy-to-use effects
- Summary
- Abstract
- Description
- Claims
- Application Information
AI Technical Summary
Problems solved by technology
Method used
Image
Examples
Embodiment 1
[0026] Step 1: Preparation of precursor solution
[0027] Dissolve polymethyl methacrylate (PMMA) solid in acetone solution with ultrasonic heating, prepare a PMMA solution with a mass concentration of 2.5%, and mix it with an equal volume of 0.5mol / L n-tetrabutyl titanate ethanol solution to prepare Precursor.
[0028] Step 2: Preparation of soft template
[0029] Weigh the prepolymer of polydimethylsiloxane (PDMS) and initiator, the mass ratio is 10:1, stir and mix; then cast on a silicon template with a strip width of 3 μm and a spacing of 1 μm, at 60 ° C Curing in an environment; After curing, the PDMS is separated from the silicon template to obtain a PDMS soft template.
[0030] Step 3: Spin coating precursor solution on soft template surface
[0031] Under the conditions of rotation speed of 4000rpm and rotation time of 30s, the precursor solution was spin-coated on the surface of the PDMS soft template to obtain a PDMS soft template with a composite film on the surf...
Embodiment 2
[0039] Step 1: Preparation of precursor solution
[0040] Dissolve polymethyl methacrylate (PMMA) solid into acetone solution with ultrasonic heating, prepare a PMMA solution with a mass concentration of 1%, and mix it with an equal volume of 0.2mol / L n-tetrabutyl titanate ethanol solution to prepare Precursor.
[0041] Step 2: Preparation of soft template
[0042] Weigh the prepolymer of polydimethylsiloxane (PDMS) and initiator, the mass ratio is 10:1, stir and mix; then cast on the silicon template with a square width of 1 μm and a spacing of 1 μm, at 80 ° C Curing in the environment; after curing, the PDMS is separated from the silicon template to obtain a PDMS soft template.
[0043] Step 3: Spin coating precursor solution on soft template surface
[0044] Under the conditions of rotation speed of 6000rpm and rotation time of 30s, the precursor solution was spin-coated on the surface of the PDMS soft template to obtain a PDMS soft template with a composite film on the ...
Embodiment 3
[0052] Step 1: Preparation of precursor solution
[0053] Solid polystyrene (PS) was heated and dissolved in acetone solution by ultrasonic heating to prepare a PS solution with a mass concentration of 1.5%, and mixed with an equal volume of 0.5 mol / L n-tetrabutyl titanate ethanol solution to prepare a precursor solution.
[0054] Step 2: Preparation of soft template
[0055]Weigh the prepolymer of polydimethylsiloxane (PDMS) and the initiator, the mass ratio is 10:1, stir and mix; then cast on the silicon template with a square width of 1 μm and a spacing of 1 μm, at 60 ° C Curing in the environment; after curing, the PDMS is separated from the silicon template to obtain a PDMS soft template.
[0056] Step 3: Spin coating precursor solution on soft template surface
[0057] Under the conditions of rotation speed of 4000rpm and rotation time of 30s, the precursor solution was spin-coated on the surface of the PDMS soft template to obtain a PDMS soft template with a composite...
PUM
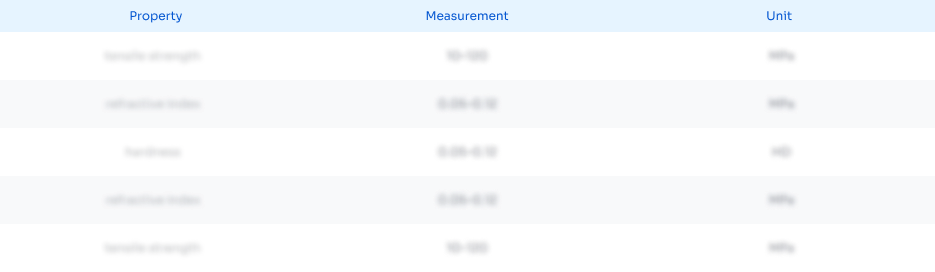
Abstract
Description
Claims
Application Information

- R&D Engineer
- R&D Manager
- IP Professional
- Industry Leading Data Capabilities
- Powerful AI technology
- Patent DNA Extraction
Browse by: Latest US Patents, China's latest patents, Technical Efficacy Thesaurus, Application Domain, Technology Topic, Popular Technical Reports.
© 2024 PatSnap. All rights reserved.Legal|Privacy policy|Modern Slavery Act Transparency Statement|Sitemap|About US| Contact US: help@patsnap.com