Coumarin borax surface cross-linking modified precipitated calcium carbonate and its preparation method, application and a kind of paper
A technology of precipitated calcium carbonate and cross-linking modification, which is applied in the direction of fibrous fillers, dyeing polymer organic compound treatment, and addition of inorganic compounds. The effect of improving the retention rate and improving the tear index
- Summary
- Abstract
- Description
- Claims
- Application Information
AI Technical Summary
Problems solved by technology
Method used
Image
Examples
Embodiment 1
[0060] Step 1: Add 0.75% (relative to the amount of PCC) coumarin into the oblique three mouths containing 90g of water, raise the temperature to 80°C, stir and disperse at 400rpm, and then add 10g of PCC;
[0061] Step 2: Add 2.5% (relative to the amount of PCC) borax into the reactor, and stir for 20 minutes;
[0062] Step 3: collecting the reaction product by centrifugation and washing and drying it;
[0063] Step 4: Grind MPCC and PCC finely with a mortar, pass through a 200-mesh copper mesh, analyze and characterize them with a scanning electron microscope, Fourier transform infrared spectrometer, elemental analyzer, etc. respectively.
[0064] The Magna IR 560 Fourier Transform Infrared Spectrometer produced by Nicolet Company of the United States was used for measurement, and the scanning range was 400 to 4000 cm -1 , scanning speed 40 times / min. The KBr tablet method is used to prepare the sample. Take an appropriate amount of the powder to be tested and mix it with ...
Embodiment 2
[0076] Step 1: Add 0.75% (relative to the amount of PCC) coumarin into the oblique three mouths containing 90g of water, raise the temperature to 80°C, stir and disperse at 400rpm, and then add 10g of PCC;
[0077] Step 2: Add 2.5% (relative to the amount of PCC) borax into the reactor, and stir for 20 minutes;
[0078] Step 3: collecting the reaction product by centrifugation and washing and drying it;
[0079] Step 4: Thaw the bleached kraft pulp soaked in water for more than 4 hours with a standard deflaker, use a beater to beat to 37°SR, add MPCC and PCC respectively after appropriate dilution, and the filling amount is 20% (based on the dry pulp amount ); refer to the method of GB / T3703-1999, make paper in a paper former; squeeze it for 1 min at a pressure of 0.4 MPa in a hydraulic press, then dry it in a drier at 97°C for 5 min, and the quantitative value of the sheet is 70 g / m 2 ;
[0080] Step 5: After drying the two hand-sheets obtained in Step 4, take a small piece...
Embodiment 3
[0083] Step 1: Add coumarin to the oblique three mouths containing 90g of water, raise the temperature to 80°C, stir and disperse at 400rpm, then add 10g of PCC; the amount of coumarin is as follows Figure 8-Figure 11 As shown, its consumption is respectively: 0.25%, 0.5%, 0.75%, 1%, 1.25%, 1.5%, 2% (relative to PCC consumption);
[0084] Step 2: Add 10% (relative to the amount of PCC) borax into the reactor, and stir for 10 minutes;
[0085] Step 3: collecting the reaction product by centrifugation and washing and drying it;
[0086] Step 4: Decompose the bleached kraft pulp soaked in water for more than 4 hours with a standard decomposer, use a beater to beat to 37°SR, add MPCC after appropriate dilution, and the filling amount is 20% (based on the dry pulp volume); refer to According to the method of GB / T3703-1999, the paper is made in a sheet forming machine; after pressing for 1 min at a pressure of 0.4 MPa in a hydraulic press, it is dried in a dryer at 97°C for 5 min,...
PUM
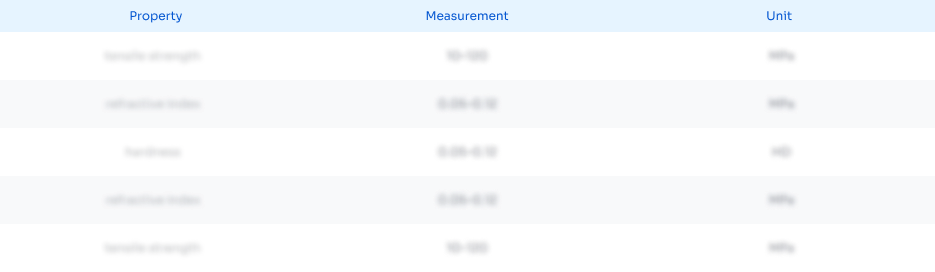
Abstract
Description
Claims
Application Information

- R&D Engineer
- R&D Manager
- IP Professional
- Industry Leading Data Capabilities
- Powerful AI technology
- Patent DNA Extraction
Browse by: Latest US Patents, China's latest patents, Technical Efficacy Thesaurus, Application Domain, Technology Topic, Popular Technical Reports.
© 2024 PatSnap. All rights reserved.Legal|Privacy policy|Modern Slavery Act Transparency Statement|Sitemap|About US| Contact US: help@patsnap.com