Aluminum alloy for preparing engine cylinder body and preparation method thereof
An engine block and aluminum alloy technology, applied in the field of aluminum alloy, can solve the problems of increasing weight density, affecting the service life of the engine, unfavorable engine cooling and heat dissipation, etc., and achieving improved strength and hardness, good room temperature performance and high temperature performance, and light specific gravity. Effect
- Summary
- Abstract
- Description
- Claims
- Application Information
AI Technical Summary
Problems solved by technology
Method used
Image
Examples
preparation example Construction
[0015] A method for preparing an aluminum alloy used to prepare an engine block provided by the present invention includes: preparing the above-mentioned various raw materials in proportion, heating and melting the various raw materials in a container, and passing the molten raw materials from the bottom of the container Inject preheated helium, remove reaction slag and scum, cast it into a mold after standing still, take it out after cooling, and obtain the primary cylinder body, and then perform quenching treatment and aging treatment on the primary cylinder body.
[0016] Specifically, the aluminum alloy for preparing the engine block and the preparation method thereof of the present invention are carried out according to the following steps:
[0017] S1 material preparation steps:
[0018] Raw materials are allocated according to the ratio, and the raw materials include: 8.5-11.5% silicon, 2-5% copper, 0.7-0.9% iron, 0.55-0.65% magnesium, 0.15-0.35% manganese, 0.6-0.65% zi...
Embodiment 1
[0040] Weigh the raw materials according to the proportion, including: 8.5% silicon, 2% copper, 0.7% iron, 0.55% magnesium, 0.15% manganese, 0.65% zinc, 0.06% nickel, 0.15% titanium, 0.25% zirconium, 0.015% erbium, 0.004% thulium, 0.015% lutetium, and the balance aluminum.
[0041] Put the raw material into the container and heat it up to 705°C until it melts, and feed the helium gas that has been preheated for 2 minutes from the bottom of the container to the raw material in the molten state. After slag, let the raw material in molten state stand for 20 minutes, then cast it into the mold, take it out after cooling, and obtain the primary cylinder; The temperature of the initial cylinder block was lowered to 200°C, and then the second cooling was performed at a cooling rate of 8°C / min; finally, the engine block was obtained by aging treatment at 180°C for 5 hours.
Embodiment 2
[0043] Weigh the raw materials according to the proportion, including: 11.5% silicon, 5% copper, 0.9% iron, 0.65% magnesium, 0.35% manganese, 0.6% zinc, 0.04% nickel, 0.1% titanium, 0.1% zirconium, 0.01% erbium, 0.002% thulium, 0.01% lutetium, and the balance aluminum.
[0044] Put the aluminum into the smelting furnace and raise the temperature to 705°C, then raise the temperature at a rate of 5°C / min until the temperature reaches 720°C, then add zirconium, titanium, lutetium, thulium, iron, erbium, nickel, silicon and manganese in sequence After all the above elements are melted, copper, magnesium and zinc are added, and helium gas that has been preheated for 3 minutes is introduced from the bottom of the melting furnace to the raw materials in the molten state. After mixing with scum, let the raw material in molten state stand for 30 minutes, then cast it into the mold, take it out after cooling, and obtain the primary cylinder body; then perform quenching treatment, and af...
PUM
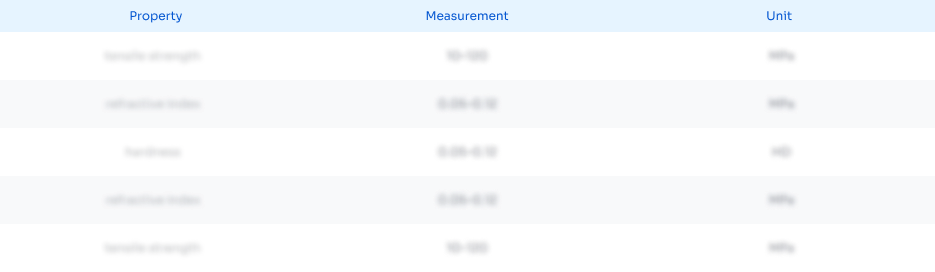
Abstract
Description
Claims
Application Information

- Generate Ideas
- Intellectual Property
- Life Sciences
- Materials
- Tech Scout
- Unparalleled Data Quality
- Higher Quality Content
- 60% Fewer Hallucinations
Browse by: Latest US Patents, China's latest patents, Technical Efficacy Thesaurus, Application Domain, Technology Topic, Popular Technical Reports.
© 2025 PatSnap. All rights reserved.Legal|Privacy policy|Modern Slavery Act Transparency Statement|Sitemap|About US| Contact US: help@patsnap.com