High-performance wood-plastic material for 3D printing forming and preparation method of wood-plastic material
A wood-plastic material and 3D printing technology, applied in the direction of additive processing, etc., can solve the problems of poor dimensional stability and low mechanical strength, achieve good dimensional stability, improve loss resistance, and expand the use range
- Summary
- Abstract
- Description
- Claims
- Application Information
AI Technical Summary
Problems solved by technology
Method used
Examples
specific Embodiment approach 1
[0026] Embodiment 1: The high-performance wood-plastic material used for 3D printing in this embodiment includes modified plant materials, engineering plastics, coupling agents or interfacial compatibilizers, lubricants, heat stabilizers and mineral fillers; The modified plant material is a plant material modified by a modifier.
specific Embodiment approach 2
[0027] Specific embodiment 2: The difference between this embodiment and specific embodiment 1 is that the modified plant material is 10-100 parts by weight, the engineering plastic or engineering plastic alloy is 20-100 parts, and the coupling agent or interface is compatible. 0-20 parts of lubricant, 0-15 parts of lubricant, 0-15 parts of heat stabilizer and 0-10 parts of mineral filler. Other steps and parameters are the same as those in the first embodiment.
specific Embodiment approach 3
[0028] Embodiment 3: This embodiment is different from Embodiment 1 in that the engineering plastic is a mixture of one or more of polyamide, polycarbonate, polyoxymethylene, modified polyphenylene ether, and thermoplastic polyester;
PUM
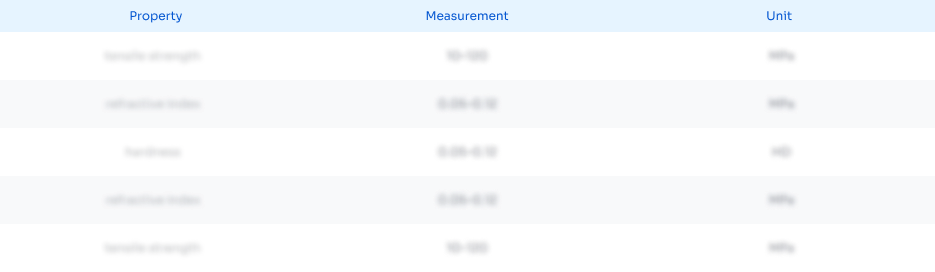
Abstract
Description
Claims
Application Information

- R&D
- Intellectual Property
- Life Sciences
- Materials
- Tech Scout
- Unparalleled Data Quality
- Higher Quality Content
- 60% Fewer Hallucinations
Browse by: Latest US Patents, China's latest patents, Technical Efficacy Thesaurus, Application Domain, Technology Topic, Popular Technical Reports.
© 2025 PatSnap. All rights reserved.Legal|Privacy policy|Modern Slavery Act Transparency Statement|Sitemap|About US| Contact US: help@patsnap.com