Preparation method of high-efficiency compound stabilizer of chlorinated paraffin
A compound stabilizer and chlorinated paraffin technology, which is applied in the chemical industry, can solve the problems of high price, large amount of addition, and insufficient increase in the thermal decomposition temperature of chlorinated paraffin.
- Summary
- Abstract
- Description
- Claims
- Application Information
AI Technical Summary
Problems solved by technology
Method used
Examples
Embodiment 1
[0020] The preparation method of chlorinated paraffin efficient composite stabilizer comprises the steps:
[0021] (1) Mix 50 parts by weight of ethylene glycol diglycidyl ether and 45 parts by weight of methyl tin evenly, add 60 parts by weight of triphenyl phosphite, stir clockwise, and after fully stirring, add the catalyst, the catalyst is sulfuric acid Mixture with glacial acetic acid, the mass ratio of sulfuric acid and glacial acetic acid is 1:3, slowly raise the temperature to 145°C, keep warm for 3h, then raise the temperature to 160°C, keep warm for 30min, cool to room temperature, and obtain solution A;
[0022] (2) At a stirring rate of 260 rpm, introduce epoxidized soybean oil into solution A at a rate of 20ml / min, continue stirring for 20 minutes, and then add chlorinated paraffin-52 to it to obtain solution B;
[0023] (3) Heat solution B to 50 ℃ ~ 60 ℃ at a slow speed, continue to stir for 15 min, add ultraviolet absorber and antioxidant, the ultraviolet absorb...
Embodiment 2
[0025] The preparation method of chlorinated paraffin efficient composite stabilizer comprises the steps:
[0026] (1) Mix 50-55 parts by weight of ethylene glycol diglycidyl ether and 45 parts by weight of methyl tin evenly, add 60 parts by weight of triphenyl phosphite, stir clockwise, after fully stirring, add catalyst, catalyst Use a mixture of sulfuric acid and glacial acetic acid, the mass ratio of sulfuric acid and glacial acetic acid is 1:3, slowly raise the temperature to 145°C, keep warm for 3h, then raise the temperature to 160°C, keep warm for 30min, cool to room temperature, and obtain solution A;
[0027] (2) At a stirring rate of 260 rpm, introduce epoxidized soybean oil into solution A at a rate of 20ml / min, continue stirring for 20 minutes, and then add chlorinated paraffin-52 to it to obtain solution B;
[0028] (3) Heat solution B to 50 ℃ at a slow speed, continue to stir for 15 min, add ultraviolet absorber and antioxidant, the ultraviolet absorber is pheny...
Embodiment 3
[0030] The preparation method of chlorinated paraffin efficient composite stabilizer comprises the steps:
[0031] (1) Mix 54 parts by weight of ethylene glycol diglycidyl ether and 50 parts by weight of methyl tin evenly, add 65 parts by weight of triphenyl phosphite, stir clockwise, and after fully stirring, add the catalyst, the catalyst is sulfuric acid Mixture with glacial acetic acid, the mass ratio of sulfuric acid to glacial acetic acid is 1:3, slowly raise the temperature to 147°C, keep it warm for 3h, then raise the temperature to 165°C, keep it warm for 30min, cool to room temperature, and get solution A;
[0032] (2) At a stirring rate of 280 rpm, introduce epoxidized soybean oil into solution A at a rate of 25ml / min, continue stirring for 25 minutes, and then add chlorinated paraffin-52 to it to obtain solution B;
[0033] (3) Heat solution B to 55 °C at a slow speed, continue to stir for 18 minutes, add ultraviolet absorber and antioxidant, the ultraviolet absorb...
PUM
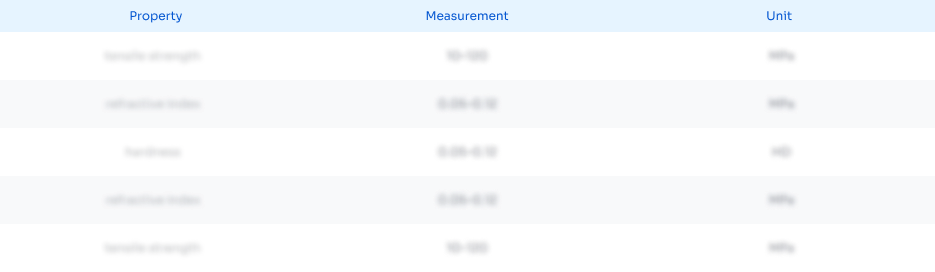
Abstract
Description
Claims
Application Information

- Generate Ideas
- Intellectual Property
- Life Sciences
- Materials
- Tech Scout
- Unparalleled Data Quality
- Higher Quality Content
- 60% Fewer Hallucinations
Browse by: Latest US Patents, China's latest patents, Technical Efficacy Thesaurus, Application Domain, Technology Topic, Popular Technical Reports.
© 2025 PatSnap. All rights reserved.Legal|Privacy policy|Modern Slavery Act Transparency Statement|Sitemap|About US| Contact US: help@patsnap.com