Modified formula of conductive master batch
A conductive masterbatch and modification technology, which is applied in the field of conductive masterbatch, can solve the problem of conductive masterbatch injection fluidity, surface appearance quality, toughness, reduction of physical properties of bending strength, conductive masterbatch injection fluidity, surface appearance quality and bending Reduced strength and other physical properties, large power consumption, etc., to achieve the effect of high carbon black content, good electrical conductivity, and low production cost
- Summary
- Abstract
- Description
- Claims
- Application Information
AI Technical Summary
Problems solved by technology
Method used
Examples
Embodiment 1
[0009] A modified formula of conductive masterbatch, which is obtained by mixing the following components in a weight ratio evenly and then putting them into a twin-screw granulator to granulate: 25-30% carbon black, 30-45% polypropylene, 1-5% glass fiber , 1-2% nano-scale iron oxide, 1-2% nano-scale zirconia, 0.5-1 part cocamide, 1-5% terpene resin, 5-10 methylimidazole, 1-5% naphthenic oil , 1-5% polyoxymethylene, 1-5% diatomaceous earth, 0.1-0.5% nano-silver powder, 1-3% cage-type silsesquioxane epoxy resin, 1-5% cross-linked carboxymethyl Cellulose, 5-10% urethane acrylate, 1-3% nano-sized aluminum triisopropoxide, 0.1-0.3% 2-hydroxy-2-methyl-1-phenyl-1-propanone, 0.1-0.3 parts Polymer flow agent and 0.1-0.3 antioxidant, the balance is polyethylene.
[0010] Embodiment one
[0011] A modified formula of conductive masterbatch, which is obtained by mixing the following components in a weight ratio evenly and then putting them into a twin-screw granulator to granulate: 28-...
PUM
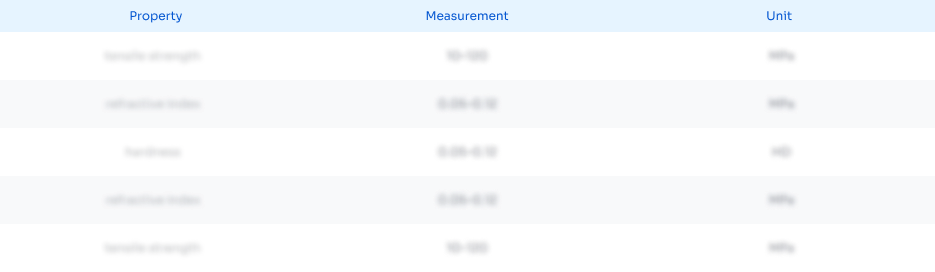
Abstract
Description
Claims
Application Information

- R&D Engineer
- R&D Manager
- IP Professional
- Industry Leading Data Capabilities
- Powerful AI technology
- Patent DNA Extraction
Browse by: Latest US Patents, China's latest patents, Technical Efficacy Thesaurus, Application Domain, Technology Topic, Popular Technical Reports.
© 2024 PatSnap. All rights reserved.Legal|Privacy policy|Modern Slavery Act Transparency Statement|Sitemap|About US| Contact US: help@patsnap.com