20Cr cam machining process
A processing technology and cam technology, which is applied in the field of 20Cr cam processing technology, can solve problems such as easy cracks in the cam, and achieve the effects of solving cracks, improving hardness and high toughness
- Summary
- Abstract
- Description
- Claims
- Application Information
AI Technical Summary
Problems solved by technology
Method used
Image
Examples
Embodiment Construction
[0021] Describe in detail below in conjunction with specific embodiment according to accompanying drawing:
[0022] A kind of 20Cr steel cam processing technology, comprises the following steps:
[0023] S1: blank forming, forming a blank with a cam profile by forging or casting;
[0024] S2: Rough turning, the two end faces and the inner hole of the cam are roughly machined on the lathe;
[0025] S3: Milling the cam profile, machining the cam profile on a milling machine or machining center;
[0026] S4: Carburizing, carburizing the surface of the cam profile;
[0027] S5: semi-finishing, semi-finishing the two end faces and inner holes of the cam on the lathe;
[0028] S6: quenching, performing quenching treatment on the cam processed in step S5;
[0029] S7: Finish turning, finishing the two end faces and the inner hole of the cam on the lathe;
[0030] S8: Coarsely grinding the cam, rough grinding the profile of the cam on the grinding machine;
[0031] S9: tempering...
PUM
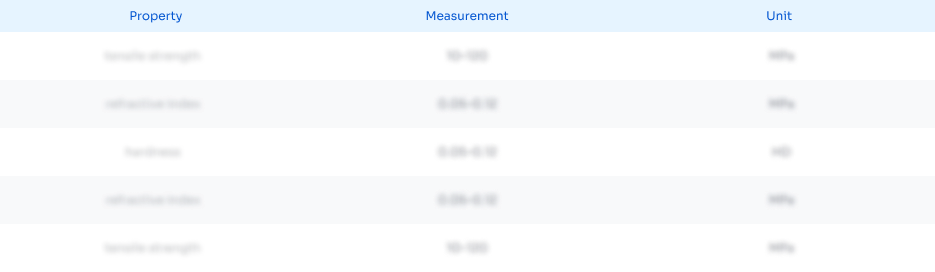
Abstract
Description
Claims
Application Information

- Generate Ideas
- Intellectual Property
- Life Sciences
- Materials
- Tech Scout
- Unparalleled Data Quality
- Higher Quality Content
- 60% Fewer Hallucinations
Browse by: Latest US Patents, China's latest patents, Technical Efficacy Thesaurus, Application Domain, Technology Topic, Popular Technical Reports.
© 2025 PatSnap. All rights reserved.Legal|Privacy policy|Modern Slavery Act Transparency Statement|Sitemap|About US| Contact US: help@patsnap.com