Method for preparing macroporous vulcanization-type hydrogenation catalyst through one-step molding
A hydrogenation catalyst and vulcanization-type technology, which is applied in the field of preparation of macroporous vulcanization-type hydrogenation catalysts, can solve the problem of low initial temperature, achieve large pore volume, broad market application prospects, and simple preparation process
- Summary
- Abstract
- Description
- Claims
- Application Information
AI Technical Summary
Problems solved by technology
Method used
Image
Examples
Embodiment 1
[0039] 1. Prepare Mo-Ni-P solution: first add 50ml of clean water to the preparation container, start the agitator, slowly add 57.2 g of molybdenum oxide, 22.4 g of basic nickel carbonate, and finally slowly add 1.27 g of phosphoric acid to avoid basic carbonic acid The salt is heated and decomposed to produce carbon dioxide bump. After adding the materials, cover tightly, then heat up to >100°C, and keep the temperature constant for 1-2 hours, until the molybdenum oxide and basic nickel carbonate are completely dissolved, and the Mo-Ni-P solution is prepared. Mo-Ni-P solution concentration is MoO 3 , 57.1g / 100ml; NiO, 9.8 g / 100ml; P, 4.0 g / 100ml;
[0040] 2. Mix 10.9 g of elemental sulfur, 2 g of kerosene, and 22 g of rapeseed oil for 15 minutes; add 5 g of Mo-Ni type EPRES external presulfurization catalyst UDS-6 (Φ3.0), heat up to 100-120 ° C, and keep the temperature for 5-15 min ; Then, add 64ml of the above-mentioned Mo-Ni-P solution, and keep the temperature at 120°C f...
Embodiment 2
[0048] 1. First, add 25ml of clean water into the preparation container, start the mixer, slowly add 9.8g of basic cobalt carbonate, 14g of citric acid, then heat up to >100°C, keep the temperature for 10-20min, and naturally cool to room temperature to obtain Co- citric acid solution. The solution concentration is CoO, 14.5 g / 100ml;
[0049] 2. Mix 10.9g of elemental sulfur, 2g of diesel oil, 22g of soybean oil, and 3g of glycerin for 5 minutes; add 5g of Co-Mo type EPRES external presulfurization catalyst FH-40B (Φ3.0), heat up to 100-120°C, and keep the temperature for 25 minutes ; Then, add 65ml of the above-mentioned Co-citric acid solution, and keep the temperature at 120°C for 25min. Then, cool and separate and remove the external presulfided catalyst FH-40B to obtain liquid mixture I;
[0050] 3. Take 50ml of water, add 4.6ml of concentrated nitric acid to dilute to obtain dilute nitric acid; then, add 5g of citric acid and 4g of urea, and then add 20g of silica sol,...
Embodiment 3
[0057] 1. First add 25ml of clean water to the preparation container, start the agitator, slowly add 9.8g of basic cobalt carbonate, 14g of citric acid, then heat up to >100°C, keep the temperature for 10-20min, and naturally cool to room temperature, the solution volume is 35ml . A Co-citric acid solution was prepared. Add ammonium heptamolybdate 18.2g then, add ammoniacal liquor (0.94g / ml specific gravity) 50ml again, prepare Co-Mo citric acid solution concentration and be MoO 3 , 21.1g / 100ml; CoO, 3.90g / 100ml;
[0058] 2. Take 12.9 g of elemental sulfur, 2.2 g of white oil, and 24 g of lard and mix for 15 minutes; add 5.0 g of oxidized Co-Mo catalyst UDS-5 (Φ3.0), raise the temperature to 100-120 ° C, and keep the temperature for 5-15 minutes; Then, add 66ml of the above-mentioned Co-Mo citric acid solution, and keep the temperature at 120°C for 25min, then cool and separate the catalyst UDS-5 to obtain liquid mixture I;
[0059] 3. Take 52ml of water, add 4.7ml of conce...
PUM
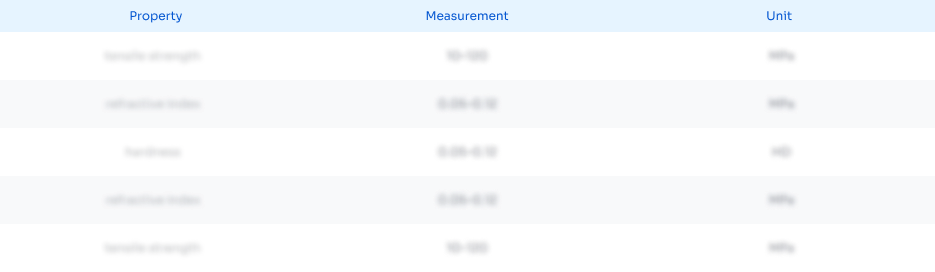
Abstract
Description
Claims
Application Information

- R&D
- Intellectual Property
- Life Sciences
- Materials
- Tech Scout
- Unparalleled Data Quality
- Higher Quality Content
- 60% Fewer Hallucinations
Browse by: Latest US Patents, China's latest patents, Technical Efficacy Thesaurus, Application Domain, Technology Topic, Popular Technical Reports.
© 2025 PatSnap. All rights reserved.Legal|Privacy policy|Modern Slavery Act Transparency Statement|Sitemap|About US| Contact US: help@patsnap.com