Sulfur-resistant catalytic combustion catalyst as well as preparation method and application
A catalytic combustion and catalyst technology, which is applied in the direction of combustion methods, physical/chemical process catalysts, molecular sieve catalysts, etc., can solve the problems of sulfur poisoning and high cost, and achieve the characteristics of not easy sintering, overcoming high temperature and easy sintering, and high catalytic activity Effect
- Summary
- Abstract
- Description
- Claims
- Application Information
AI Technical Summary
Problems solved by technology
Method used
Image
Examples
Embodiment 1
[0024] The crushed and sieved γ-Al 2 o 3 The carrier (16-30 mesh) was dried in an oven at 110° C. for 4 hours. Weigh 4.03gCu(NO 3 ) 2 ·3H 2 O, 9.70gCo(NO 3 ) 2 ·6H 2 O, in which the atomic ratio of copper to cobalt is 1:2, add a certain amount of deionized water to dissolve and configure a 25ml solution. 20g γ-Al 2 o 3 Immerse the equal volume of the carrier in the above mixed solution, ultrasonically vibrate at an ultrasonic frequency of 25kHz for 40min, dry at 110°C for 13h, and bake at 600°C in a muffle furnace for 5h to obtain a Cu-Co-O / γ-Al with a loading capacity of 20%. 2 o 3 catalyst.
Embodiment 2
[0026] The crushed and sieved 5A molecular sieve carrier (20-40 mesh) was dried in an oven at 120° C. for 4 hours. Weigh 2.01gCu(NO 3 ) 2 ·3H 2 O, 4.35gCo(NO 3 ) 2 ·6H 2 O, in which the atomic ratio of copper to cobalt is 1:2, add a certain amount of deionized water to dissolve and configure a 28ml solution. Immerse 20g of 5A molecular sieve carrier in equal volume in the above mixed solution, ultrasonically vibrate at an ultrasonic frequency of 20kHz for 100min, dry at 110°C for 12h, and bake at 500°C in a muffle furnace for 5h to obtain a 10% Cu-Co-O / 5A molecular sieve catalyst. The SEM image of the catalyst surface is attached figure 1 . Depend on figure 1 It can be seen that the copper oxide and cobalt oxide crystal particles on the surface of the catalyst are small and evenly distributed, and the catalyst still has the original pore structure of the molecular sieve after loading.
Embodiment 3
[0028] The crushed and sieved γ-Al 2 o 3 The carrier (16-30 mesh) was dried in an oven at 110° C. for 6 hours. Weigh 4.03gCu(NO 3 )2·3H 2 O, 9.70gCo(NO 3 ) 2 ·6H 2 O, 7.74gCe(NO 3 ) 2 ·6H 2 O, wherein the atomic ratio of copper, cobalt and cerium is 1:2:1, add a certain amount of deionized water to dissolve, and mix to obtain the active component solution. Immerse 20g of γ-Al2O3 carrier in equal volume in the above mixed solution, ultrasonically vibrate at an ultrasonic frequency of 28kHz for 35min, dry at 120°C for 10h, and bake in a muffle furnace at 600°C for 5h to obtain CeO with a loading capacity of 20%. 2 / Cu-Co-O / γ-Al 2 o 3 catalyst. The SEM image of the catalyst surface is attached figure 2 . Depend on figure 2 It can be seen that the catalyst still has a porous structure of aluminum oxide after loading.
PUM
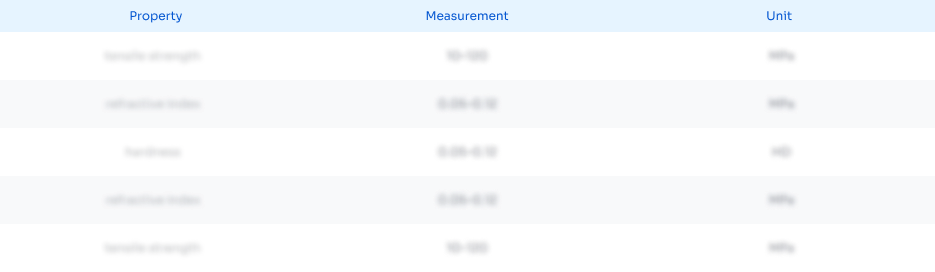
Abstract
Description
Claims
Application Information

- R&D
- Intellectual Property
- Life Sciences
- Materials
- Tech Scout
- Unparalleled Data Quality
- Higher Quality Content
- 60% Fewer Hallucinations
Browse by: Latest US Patents, China's latest patents, Technical Efficacy Thesaurus, Application Domain, Technology Topic, Popular Technical Reports.
© 2025 PatSnap. All rights reserved.Legal|Privacy policy|Modern Slavery Act Transparency Statement|Sitemap|About US| Contact US: help@patsnap.com