Method for preparing high-purity vanadium pentoxide by using vanadium-contained material
A technology for vanadium pentoxide and materials, applied in the field of vanadium extraction, can solve the problems of low chlorination efficiency, high production cost and high chlorination temperature, and achieve the effects of reducing the generation of three wastes, less environmental pollution and mild process conditions
- Summary
- Abstract
- Description
- Claims
- Application Information
AI Technical Summary
Problems solved by technology
Method used
Image
Examples
Embodiment 1
[0081] The mass percentages of some components in the vanadium slag used in this embodiment are V8.90%, Cr1.37%, Al1.54%, Fe23.34%, Si6.46%, Ca1.05%, Mg1.75%.
[0082] The method for preparing high-purity vanadium pentoxide by using the vanadium slag comprises the following steps:
[0083] (1) Chlorination: get 105.5g of vanadium slag roasted at 900°C for 2h and mix with anhydrous aluminum trichloride and sodium chloride, wherein the molar ratio of vanadium pentoxide and anhydrous aluminum chloride in the vanadium slag is 1: 3. The molar ratio of anhydrous aluminum trichloride to sodium chloride is 3:2, the reaction temperature is 170°C, the nitrogen atmosphere is used as the carrier gas, and the reaction takes 2 hours to obtain vanadyl trichloride gas and alumina residue. The vanadium gas was condensed, and 20.89 g of vanadium oxychloride liquid was collected;
[0084] (2) Hydrolysis: hydrolyze 5mL vanadium oxychloride in 110mL dilute ammonia water (1+2), filter to obtain am...
Embodiment 2
[0089] The mass percentages of some components in the vanadium slag used in this embodiment are V5.08%, Cr5.20%, Al5.68%, Fe17.52%, Si14.80%, Ca0.50%, Mg6.19%.
[0090] The method for preparing high-purity vanadium pentoxide by using the vanadium slag comprises the following steps:
[0091] (1) Chlorination: The vanadium slag raw material is mixed with anhydrous aluminum trichloride and sodium chloride after roasting at 800°C for 1 hour, wherein the molar ratio of vanadium pentoxide to aluminum chloride in the vanadium slag is 1:1, without The molar ratio of aluminum trichloride to sodium chloride in water is 7:3, the reaction temperature is 160°C, the helium atmosphere is used as the carrier gas, and the reaction is carried out for 1 hour to obtain vanadyl trichloride gas and alumina residue, and oxychloride is collected by condensation. Vanadium liquid;
[0092] (2) Hydrolysis: 5mL of vanadyl trichloride is hydrolyzed in 50mL of high-purity water, and liquid-solid separatio...
Embodiment 3
[0097] The mass percentages of some components in the vanadium slag used in this embodiment are V8.06%, Cr1.35%, Al1.43%, Fe26.30%, Si7.03%, Ca1.07%, Mg1.68%.
[0098] The method for preparing high-purity vanadium pentoxide by using the vanadium slag comprises the following steps:
[0099] (1) Chlorination: the vanadium slag raw material is mixed with anhydrous aluminum trichloride and sodium chloride after roasting at 900°C for 3 hours, wherein the molar ratio of vanadium pentoxide to aluminum chloride in the vanadium slag is 1:2, without The molar ratio of aluminum trichloride to sodium chloride in water is 4:1, the reaction temperature is 170°C, the argon atmosphere is used as the carrier gas, and the reaction takes 3.5 hours to obtain vanadyl trichloride gas and alumina residue, and the trichloride is collected by condensation. Vanadyl liquid;
[0100] (2) Hydrolysis: 5mL of vanadyl trichloride is hydrolyzed in 100mL of ammonium chloride (pH is 9) aqueous solution, filter...
PUM
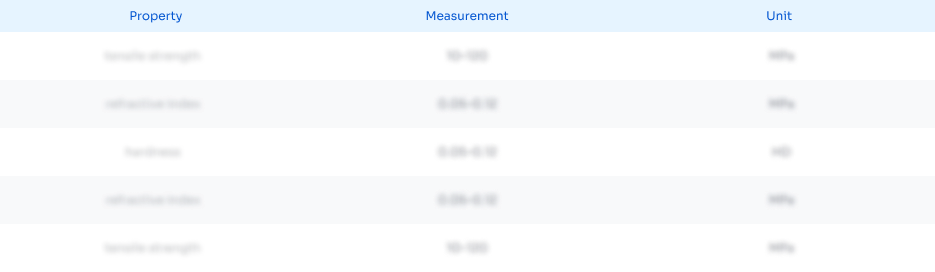
Abstract
Description
Claims
Application Information

- R&D
- Intellectual Property
- Life Sciences
- Materials
- Tech Scout
- Unparalleled Data Quality
- Higher Quality Content
- 60% Fewer Hallucinations
Browse by: Latest US Patents, China's latest patents, Technical Efficacy Thesaurus, Application Domain, Technology Topic, Popular Technical Reports.
© 2025 PatSnap. All rights reserved.Legal|Privacy policy|Modern Slavery Act Transparency Statement|Sitemap|About US| Contact US: help@patsnap.com