Graphene anticorrosive paint and preparation method thereof
An anti-corrosion coating and graphene technology, applied in the field of coatings, can solve problems such as the development of solvent-free anti-corrosion coatings without precedent, and achieve the effects of enhancing toughness, reducing shrinkage stress, and simple preparation methods
- Summary
- Abstract
- Description
- Claims
- Application Information
AI Technical Summary
Problems solved by technology
Method used
Examples
preparation example Construction
[0033] The invention also provides a preparation method of the graphene anticorrosion coating. The preparation method comprises the following steps:
[0034] S1, mixing graphene, reactive diluent and first auxiliary agent to obtain graphene slurry, wherein the first auxiliary agent includes wetting agent, leveling agent, defoamer and anti-settling agent;
[0035] S2, mixing graphene slurry, epoxy resin, titanium dioxide, barium sulfate, zinc phosphate and the second auxiliary agent to obtain a prefabricated coating, wherein the second auxiliary agent includes an adhesion promoter, a drier, a thixotropic agent;
[0036] S3, mixing the prefabricated coating with a curing agent to obtain the graphene anti-corrosion coating.
[0037]In step S1, the graphene, the reactive diluent and the first auxiliary agent may be mixed and dispersed for 5 minutes to 100 minutes by a high-speed shearing machine at a speed of 1000 rad / min to 3000 rad / min.
[0038] In step S2, the components are...
Embodiment 1
[0042] A kind of graphene anticorrosion coating, is made up of following components according to mass percentage: 0.5 parts of graphene powder, 48 parts of bisphenol A epoxy resins, 7 parts of butyl glycidyl ethers, 12 parts of titanium dioxide, 14 parts of barium sulfate, 7 parts of zinc phosphate, 1.2 parts of defoamer, 2.3 parts of anti-settling agent, 8 parts of cashew oil modified phenalkamine curing agent. Wherein, the defoamer is a silicone defoamer, and the anti-settling agent is an amide wax.
[0043] The preparation method of this graphene anticorrosion coating is as follows:
[0044] (1) Preparation of graphene slurry: blend graphene, butyl glycidyl ether, and defoamer, and disperse for 60 minutes at a speed of 3000 rad / min with a high-speed shearing machine to obtain graphene slurry.
[0045] (2) Mix and stir the graphene slurry prepared in step (1) with epoxy resin, titanium dioxide, barium sulfate, zinc phosphate and the remaining additives in proportion, and gr...
Embodiment 2
[0048] A graphene anti-corrosion coating, which is composed of the following components in terms of mass percentage: 1.2 parts of graphene powder, 40 parts of bisphenol F epoxy resin, 10 parts of tert-butyl glycidyl ether, 8 parts of titanium dioxide, and 5 parts of barium sulfate , 15 parts of zinc phosphate, 1.8 parts of defoamer, 1 part of anti-settling agent, 1 part of wetting and dispersing agent, 17 parts of Mannich alkali curing agent. Among them, the defoaming agent is a silicone defoaming agent, the anti-settling agent is a hydrogenated castor oil derivative anti-settling agent, and the wetting and dispersing agent is a polyoxyethylene fatty alcohol ether wetting and dispersing agent.
[0049] The preparation method of this graphene anticorrosion coating is as follows:
[0050] (1) Preparation of graphene slurry: blend graphene with tert-butyl glycidyl ether, defoamer and wetting agent, and disperse for 60 minutes at a speed of 3000 rad / min with a high-speed shearing ...
PUM
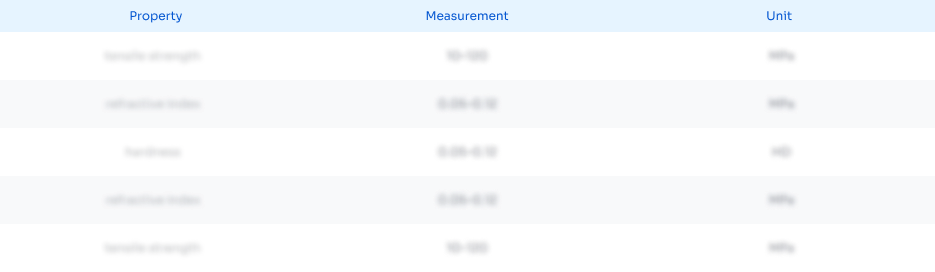
Abstract
Description
Claims
Application Information

- R&D
- Intellectual Property
- Life Sciences
- Materials
- Tech Scout
- Unparalleled Data Quality
- Higher Quality Content
- 60% Fewer Hallucinations
Browse by: Latest US Patents, China's latest patents, Technical Efficacy Thesaurus, Application Domain, Technology Topic, Popular Technical Reports.
© 2025 PatSnap. All rights reserved.Legal|Privacy policy|Modern Slavery Act Transparency Statement|Sitemap|About US| Contact US: help@patsnap.com