Synthetic process of naphthol
A synthesis process, a technology of naphthol, is applied in the field of synthesis technology of organic compounds, and can solve the problems of decreasing reaction speed, reducing sulfuric acid, a large amount of waste water and waste salt, etc., and achieving the effects of simplified operation, high utilization rate and less waste water volume.
- Summary
- Abstract
- Description
- Claims
- Application Information
AI Technical Summary
Problems solved by technology
Method used
Image
Examples
Embodiment 1
[0032] In a 1000-liter four-necked flask (equipped with a dropping funnel, the reflux tube is installed on the dropping funnel), add 129.3 g of naphthalene (content 99%, 1 mol) and 100 g of 1, 2-dichloroethane, and heat up to 60- 70°C, after the naphthalene is completely dissolved, add 100g (1mol) of sulfuric acid with a mass fraction of 98% into the flask dropwise within a few minutes. 2-dichloroethane and water, adjust the speed of 1, 2-dichloroethane in the lower layer to return to the flask to keep the reaction temperature at 110-120°C, take a sample for analysis after reflux for 5-6 hours, and the residual acid is reduced to 4 %, the residual naphthalene drops to about 2%, stop reflux, evaporate the remaining 1,2-dichloroethane in the flask, cool down to below 100°C after steaming, slowly add 210g of sodium sulfite aqueous solution with a mass fraction of 30% to neutralize Naphthalenesulfonic acid, collect the generated sulfur dioxide gas for subsequent acidification of s...
Embodiment 2
[0034] In a 1000-liter four-necked flask (equipped with a dropping funnel, the reflux tube is installed on the dropping funnel), add 129.3 g of naphthalene (content 99%, 1 mol) and 100 g of 1, 2-dichloroethane, and heat up to 60- 70°C, after the naphthalene is completely dissolved, add 103g (1.03mol) of sulfuric acid with a mass fraction of 98% into the flask dropwise within a few minutes, heat up to 110-120°C for reflux reaction, and collect the refluxed 1 , 2-dichloroethane and water, adjust the rate at which the lower 1,2-dichloroethane refluxes into the flask to keep the reaction temperature at 110-120°C, and take samples for analysis after 5-6 hours of reflux, and the residual acid drops to 4% or less, the residual naphthalene drops to about 1.8%, stop reflux, evaporate the remaining 1, 2-dichloroethane in the flask, cool down to below 100°C after steaming, slowly add 210g of sodium sulfite aqueous solution with a mass fraction of 30% and naphthalenesulfonic acid, collect...
Embodiment 3
[0036] In a 1000-liter four-necked flask (equipped with a dropping funnel, the reflux tube is installed on the dropping funnel), add 129.3 g of naphthalene (content 99%, 1 mol) and 100 g of 1, 2-dichloroethane, and heat up to 60- 70°C, after the naphthalene is completely dissolved, add 105g (1.05mol) of sulfuric acid with a mass fraction of 98% into the flask dropwise within a few minutes, and raise the temperature to 110-120°C for reflux reaction after the addition, and collect the refluxed 1 , 2-dichloroethane and water, adjust the rate at which the lower 1,2-dichloroethane refluxes into the flask to keep the reaction temperature at 110-120°C, and take samples for analysis after reflux for 5-6 hours, and the residual acid drops to 4% or less, the residual naphthalene drops to about 1.6%, stop reflux, evaporate the remaining 1, 2-dichloroethane in the flask, cool down to below 100°C after steaming, and slowly add 210g of sodium sulfite aqueous solution with a mass fraction of ...
PUM
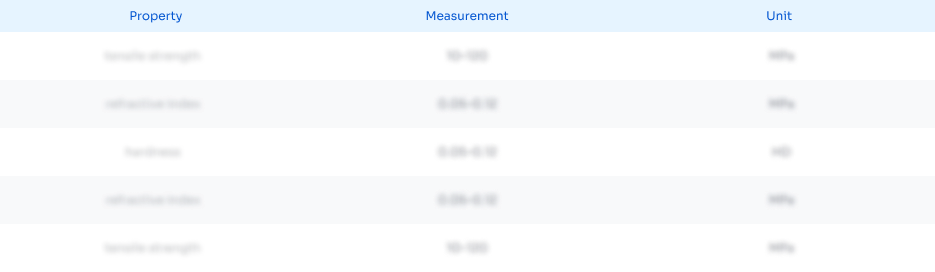
Abstract
Description
Claims
Application Information

- Generate Ideas
- Intellectual Property
- Life Sciences
- Materials
- Tech Scout
- Unparalleled Data Quality
- Higher Quality Content
- 60% Fewer Hallucinations
Browse by: Latest US Patents, China's latest patents, Technical Efficacy Thesaurus, Application Domain, Technology Topic, Popular Technical Reports.
© 2025 PatSnap. All rights reserved.Legal|Privacy policy|Modern Slavery Act Transparency Statement|Sitemap|About US| Contact US: help@patsnap.com