Copper plating solution for plate roller and preparation method of copper plating solution
The technology of a copper plating solution and plate roller is applied in the field of plate roller copper plating solution and its preparation, which can solve the problems of insufficient smoothness of the plating layer, low brightness of the plating layer, poor surface uniformity, etc., and achieve simple preparation method, good surface uniformity, good weather resistance
- Summary
- Abstract
- Description
- Claims
- Application Information
AI Technical Summary
Problems solved by technology
Method used
Image
Examples
Embodiment 1
[0019] A plate roller copper plating solution, made of the following raw materials in parts by weight: including 56 parts of copper sulfate pentahydrate, 30 parts of hydroxybutylene diphosphonic acid, 33 parts of methylaminodimethylidene phosphonic acid, and 26 parts of tripotassium citrate , 24 parts of trisodium citrate, 12 parts of polyethyleneimine, 40 parts of boric acid, 11 parts of sodium hydroxide, 13 parts of glycerin, 10 parts of pyrophosphate, 11 parts of thiosulfate, and 11 parts of sulfite , 10 parts of sodium lauryl sulfate, 9 parts of sodium 2-ethylhexanol sulfate, 9 parts of dioctyl sodium sulfosuccinate, 12 parts of sodium phosphate diester and 100 parts of water.
[0020] A preparation method for plate roller copper plating solution, comprising the following steps:
[0021] 1) Take 100 parts of water and pour it into the pot, and heat it to 50°C to make warm water, set aside;
[0022] 2) Get 40% of the warm water total amount after heating in step 1) and put...
Embodiment 2
[0028] A plate roller copper plating solution, made of the following raw materials in parts by weight: including 40 parts of copper sulfate pentahydrate, 50 parts of hydroxybutylene diphosphonic acid, 41 parts of methylaminodimethylidene phosphonic acid, and 38 parts of tripotassium citrate , 30 parts of trisodium citrate, 18 parts of polyethyleneimine, 60 parts of boric acid, 19 parts of sodium hydroxide, 17 parts of glycerol, 14 parts of pyrophosphate, 15 parts of thiosulfate, and 17 parts of sulfite , 16 parts of sodium lauryl sulfate, 13 parts of sodium 2-ethylhexanol sulfate, 15 parts of dioctyl sodium sulfosuccinate, 18 parts of sodium phosphate diester and 160 parts of water.
[0029] A preparation method for plate roller copper plating solution, comprising the following steps:
[0030] 1) Take 160 parts of water and pour it into the pot, and heat it to 60°C to make warm water, set aside;
[0031] 2) Get 40% of the warm water total amount after heating in step 1) and p...
Embodiment 3
[0037] A plate copper plating solution, made of the following raw materials in parts by weight: including 48 parts of copper sulfate pentahydrate, 40 parts of hydroxybutylene diphosphonic acid, 37 parts of methylaminodimethylidene phosphonic acid, and 32 parts of tripotassium citrate , 27 parts of trisodium citrate, 15 parts of polyethyleneimine, 50 parts of boric acid, 15 parts of sodium hydroxide, 15 parts of glycerol, 12 parts of pyrophosphate, 13 parts of thiosulfate, and 14 parts of sulfite , 13 parts of sodium lauryl sulfate, 11 parts of sodium 2-ethylhexanol sulfate, 12 parts of dioctyl sodium sulfosuccinate, 15 parts of sodium phosphate diester and 130 parts of water.
[0038] A preparation method for plate roller copper plating solution, comprising the following steps:
[0039] 1) Take 130 parts of water and pour it into the pot, and heat it to 55°C to make warm water, set aside;
[0040] 2) Get 40% of the warm water total amount after heating in step 1) and put it i...
PUM
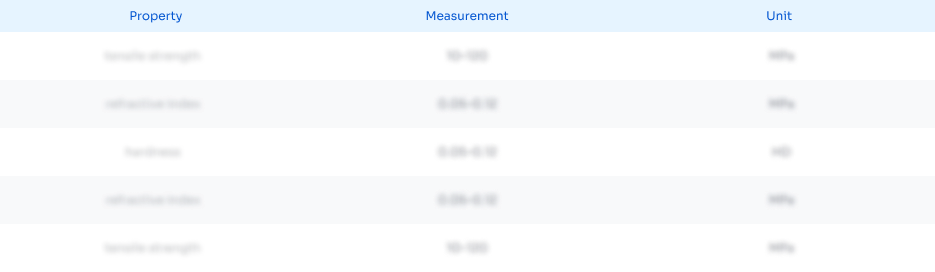
Abstract
Description
Claims
Application Information

- R&D Engineer
- R&D Manager
- IP Professional
- Industry Leading Data Capabilities
- Powerful AI technology
- Patent DNA Extraction
Browse by: Latest US Patents, China's latest patents, Technical Efficacy Thesaurus, Application Domain, Technology Topic, Popular Technical Reports.
© 2024 PatSnap. All rights reserved.Legal|Privacy policy|Modern Slavery Act Transparency Statement|Sitemap|About US| Contact US: help@patsnap.com