Rare earth magnesium alloy fabrication method
A processing method and rare earth magnesium technology, which are applied in the processing field of rare earth magnesium alloys, can solve the problems of poor high temperature mechanical properties, difficult to use for a long time, and decreased strength of magnesium alloys, and achieve good high temperature resistance mechanical properties, prolong service life and structure. symmetrical effect
- Summary
- Abstract
- Description
- Claims
- Application Information
AI Technical Summary
Problems solved by technology
Method used
Image
Examples
Embodiment 1
[0038] A processing method for a rare earth magnesium alloy, comprising the steps of:
[0039] Step 1. Using high-energy ball milling for 5 hours to obtain a mixed powder, the mixed powder is placed in a crucible of a vacuum induction melting furnace;
[0040] Step 2, vacuumize the vacuum induction melting furnace until the vacuum pressure is -50MPa, and process for 20min;
[0041] Step 3, heating the crucible under vacuum conditions at a heating temperature of 550° C. and keeping it warm for 40 minutes to obtain alloy soup;
[0042] Step 4. Under the protection of an inert gas, pour lithium nanopowder into the alloy soup, and mix evenly, then extrude, wait for it to cool, and shape it by extrusion forging to form a magnesium alloy. The extrusion ratio during this time is 10:1, and the pressure of described extrusion is 650T, and the speed of extrusion is 0.3mm / s;
[0043] Wherein, the lithium element and the aluminum element undergo a combination reaction to precipitate an ...
Embodiment 2
[0047] A processing method for a rare earth magnesium alloy, comprising the steps of:
[0048] Step 1, using high-energy ball milling of magnesium-yttrium alloy, magnesium-neodymium alloy, magnesium-dysprosium alloy, and magnesium-aluminum alloy for 6 hours to obtain a mixed powder, and then placing the mixed powder in a crucible of a vacuum induction melting furnace;
[0049] Step 2, vacuumize the vacuum induction melting furnace until the vacuum pressure is -20MPa, and process for 30min;
[0050] Step 3, heating the crucible under vacuum conditions at a heating temperature of 600°C and keeping it warm for 60 minutes to obtain alloy soup;
[0051] Step 4. Under the protection of an inert gas, pour lithium nanopowder into the alloy soup, and mix evenly, then extrude, wait for it to cool, and shape it by extrusion forging to form a magnesium alloy. The extrusion ratio during the time is 15:1, and the pressure of described extrusion is 700T, and the speed of extrusion is 0.9mm / ...
Embodiment 3
[0056] A processing method for a rare earth magnesium alloy, comprising the steps of:
[0057] Step 1. Using high-energy ball milling for 5.5 hours to obtain a mixed powder, the mixed powder is placed in a crucible of a vacuum induction melting furnace;
[0058]Step 2, vacuumize the vacuum induction melting furnace until the vacuum pressure is -30MPa, and process for 25min;
[0059] Step 3. Under vacuum conditions, the crucible is heated to a heating temperature of 575° C. and kept for 50 minutes to obtain an alloy soup;
[0060] Step 4. Under the protection of an inert gas, pour the lithium nanopowder into the alloy soup, mix it evenly, then extrude it, wait for it to cool, and shape it by extrusion forging to form a magnesium alloy, wherein the The extrusion pressure is 600T. The extrusion ratio during extrusion is 13:1, and the extrusion speed is 0.6mm / s; the inert gas is argon.
[0061] Wherein, the lithium element and the aluminum element undergo a combination reaction...
PUM
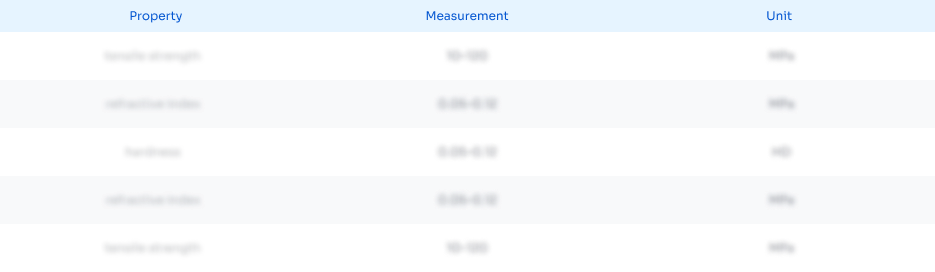
Abstract
Description
Claims
Application Information

- R&D Engineer
- R&D Manager
- IP Professional
- Industry Leading Data Capabilities
- Powerful AI technology
- Patent DNA Extraction
Browse by: Latest US Patents, China's latest patents, Technical Efficacy Thesaurus, Application Domain, Technology Topic, Popular Technical Reports.
© 2024 PatSnap. All rights reserved.Legal|Privacy policy|Modern Slavery Act Transparency Statement|Sitemap|About US| Contact US: help@patsnap.com