Treatment system and method for vanadium extraction tailings
A technology for extracting vanadium tailings and inlet, which is applied in the field of treatment systems for vanadium extraction tailings, and can solve problems such as less research
- Summary
- Abstract
- Description
- Claims
- Application Information
AI Technical Summary
Problems solved by technology
Method used
Image
Examples
Embodiment 1
[0054] Vanadium extraction tailings (TFe 38wt%, TiO 2 12wt%), titanium concentrate (TiO 2 45wt%), anthracite and then pelletized in a disc granulator to obtain pellets. Wherein, the mass ratio of each component is: vanadium extraction tailings: titanium concentrate: anthracite = 100:60:20. After the pellets are dried, they are reduced and roasted in a rotary hearth furnace at 1350° C. to obtain metallized pellets. Then, the metallized pellets are subjected to grinding and magnetic separation using a linkage device of a ball mill and a magnetic separator to obtain metallic iron powder and titanium slag. The iron grade in the obtained metal iron powder is 97.8%, and the recovery rate is 97.5%; in the titanium slag, TiO 2 The mass fraction is 55.3%, and the recovery rate is 98.8%.
Embodiment 2
[0056] Vanadium extraction tailings (TFe 30wt%, TiO 2 15wt%), titanium concentrate (TiO 2 47wt%) and coke are mixed evenly, and then briquetting is carried out by a roller briquetting machine to obtain pellets. Wherein, the mass ratio of each component is: vanadium extraction tailings: titanium concentrate: coke = 100:100:25. After the pellets are dried, they are reduced and roasted in a rotary kiln at 1400°C to obtain metallized pellets. Then, the metallized pellets are subjected to grinding and magnetic separation using a linkage device of a ball mill and a magnetic separator to obtain metallic iron powder and titanium slag. The iron grade in the obtained metal iron powder is 98.6%, and the recovery rate is 98.3%; in the titanium slag, TiO 2 The mass fraction is 58.4%, and the recovery rate is 99.3%.
Embodiment 3
[0058] Vanadium extraction tailings (TFe 35wt%, TiO 2 19wt%), titanium concentrate (TiO 2 50wt%) and semi-coke are mixed and pelletized in a disc granulator to obtain pellets. Wherein, the mass ratio of each component is: vanadium extraction tailings: titanium concentrate: semi-coke = 100:150:30. After the pellets are dried, they are reduced and roasted in a tunnel kiln at 1450°C to obtain metallized pellets. Then, the metallized pellets are subjected to grinding and magnetic separation using a linkage device of a ball mill and a magnetic separator to obtain metallic iron powder and titanium slag. The iron grade in the obtained metal iron powder is 99.1%, and the recovery rate is 98.6%; in the titanium slag, TiO 2 The mass fraction is 60.6%, and the recovery rate is 99.8%.
PUM
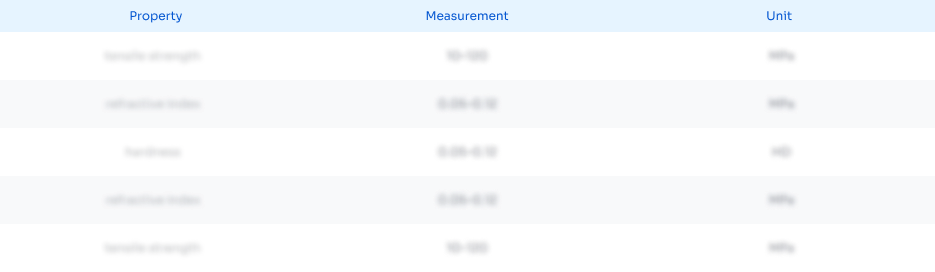
Abstract
Description
Claims
Application Information

- R&D
- Intellectual Property
- Life Sciences
- Materials
- Tech Scout
- Unparalleled Data Quality
- Higher Quality Content
- 60% Fewer Hallucinations
Browse by: Latest US Patents, China's latest patents, Technical Efficacy Thesaurus, Application Domain, Technology Topic, Popular Technical Reports.
© 2025 PatSnap. All rights reserved.Legal|Privacy policy|Modern Slavery Act Transparency Statement|Sitemap|About US| Contact US: help@patsnap.com