Preparation method of heavy corrosion protection primer resin
A heavy-duty anti-corrosion primer and resin technology, applied in the field of coatings, can solve the problems of reduced bonding force between the coating film and the substrate, coating damage, anti-corrosion performance, poor toughness, etc., and achieve excellent medium resistance and anti-corrosion performance. Medium resistance and corrosion resistance, excellent effect of corrosion resistance
- Summary
- Abstract
- Description
- Claims
- Application Information
AI Technical Summary
Problems solved by technology
Method used
Image
Examples
Embodiment 1
[0035] Add 62g of EPN-1179, 8g of n-butyl acetate, and 12g of cyclohexanone into the reaction flask, raise the temperature to 95°C under the protection of nitrogen, and start to drop the mixture of 5.7g of γ-aminopropyltriethoxysilane and 18g of xylene, After 2 hours of dropwise addition, heat preservation was carried out for 3 hours, the temperature was lowered, and the material was discharged for subsequent use to obtain modified resin A (silane-modified novolac epoxy resin).
[0036] Add 92g of E-20, 23g of coconut oleic acid, 10g of xylene and 60g of cyclohexanone into another reaction flask, raise the temperature to 160°C under the protection of nitrogen, keep the temperature for 10 hours, cool down, discharge the material for later use, and obtain a modified resin B (ring-opening epoxy resin).
[0037] Add 52g of modified resin A, 26g of modified resin B, 8.2g of γ-(2,3-epoxypropoxy)propyltrimethoxysilane, 15.5g of polypropylene glycol diglycidyl ether and 41g of methyli...
Embodiment 2
[0039] Add 35g EPN-1179, 28g EPN-1138, 14g n-butyl acetate, 20g cyclohexanone into the reaction flask, raise the temperature to 95°C under the protection of nitrogen, and start to drop 10.6g N-phenyl-α-aminomethyl The mixture of triethoxysilane and 12g of xylene was added dropwise for 2 hours and then kept for 3 hours, cooled and discharged for later use to obtain modified resin A (silane-modified novolac epoxy resin).
[0040] Add 122g of E-12, 18g of soy oil, 30g of xylene and 50g of cyclohexanone into another reaction flask, raise the temperature to 155°C under the protection of nitrogen, keep it warm for 10 hours, cool down, discharge the material for later use, and obtain modified resin B (ring-opening epoxy resin).
[0041] Add 47g of modified resin A, 32g of modified resin B, 5g of dodecafluoroheptylpropyltrimethoxysilane, 4g of γ-mercaptopropyltrimethoxysilane, and 12g of 1,6-hexanediol diglycidyl into the packaging barrel Ether and 48g n-pentyl acetate, obtain the he...
Embodiment 3
[0043] Add 70g of GY-289, 9g of n-butyl acetate, and 18g of cyclohexanone into the reaction flask, raise the temperature to 95°C under the protection of nitrogen, and start to drop 3.3g of γ-aminopropyltriethoxysilane, 2.9g of N-β -(Aminoethyl)-γ-aminopropylmethyldimethoxysilane and 22g xylene mixture, after 2 hours of dropwise addition, keep warm for 3 hours, cool down, discharge for later use, and obtain modified resin A (silane modified novolac epoxy resin).
[0044] Add 64gE-12, 33gE-20, 21g soy oil, 17g xylene and 55g cyclohexanone to another reaction flask, raise the temperature to 160°C under the protection of nitrogen, keep it warm for 10 hours, cool down, discharge the material for later use, and obtain Modified resin B (ring-opening epoxy resin).
[0045]Add 60g of modified resin A, 33g of modified resin B, 12.1g of γ-(2,3-epoxypropoxy)propyltrimethoxysilane, 6.3g of polypropylene glycol diglycidyl ether, 6.7g of phenyl Glycidyl ether and 42g pimelinketone were mec...
PUM
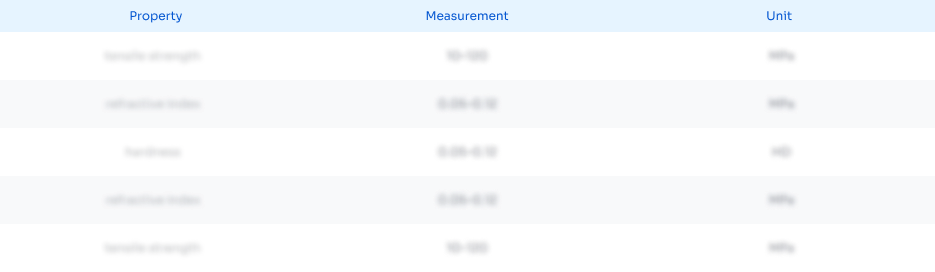
Abstract
Description
Claims
Application Information

- R&D Engineer
- R&D Manager
- IP Professional
- Industry Leading Data Capabilities
- Powerful AI technology
- Patent DNA Extraction
Browse by: Latest US Patents, China's latest patents, Technical Efficacy Thesaurus, Application Domain, Technology Topic, Popular Technical Reports.
© 2024 PatSnap. All rights reserved.Legal|Privacy policy|Modern Slavery Act Transparency Statement|Sitemap|About US| Contact US: help@patsnap.com