Environment-friendly ternary copolymerized segmented organic silicone finishing agent and preparation method thereof
A ternary copolymerization block, environmentally friendly technology, applied in the direction of fiber type, fiber treatment, improved hand fiber, etc., can solve the problems of affecting production efficiency, slow removal of isopropanol, large resistance to stirring, etc. High efficiency, stable quality, avoid the effect of glue linking
- Summary
- Abstract
- Description
- Claims
- Application Information
AI Technical Summary
Problems solved by technology
Method used
Image
Examples
Embodiment 1
[0030] (1) Add hydrogen-containing silicone oil with a molecular weight of 10000, allyl epoxy polyether with a molecular weight of 400, and isopropanol into the reaction kettle, start stirring, and raise the temperature to 80-83°C, react for 6 hours, and obtain the molecular weight It is 10800-end epoxy polyether silicone oil. React 500g of epoxy-terminated polyether silicone oil with a molecular weight of 10800, 22.2g of ED-600, 7.5g of T-403, and 353g of isopropanol at 80-83°C for 7 hours, and then distill at this temperature under normal pressure. At this time, A large number of fractions are distilled out, observe the distillate receiving tank, when 120g of isopropanol is evaporated, add 90g of dipropylene glycol; continue distillation at atmospheric pressure, after 240g of isopropanol is evaporated, then add 90g of dipropylene glycol, at this time change to decompression Distill (-0.08MPa), heat up to 95°C to 100°C until no fraction is distilled, and the total isopropanol...
Embodiment 2
[0033] (1) Add terminal hydrogen-containing silicone oil with a molecular weight of 7000, allyl epoxy polyether with a molecular weight of 500, and isopropanol into the reaction kettle, start stirring, and raise the temperature to 80-83°C, react for 6 hours, and obtain a molecular weight It is 9000-end epoxy polyether silicone oil. React 500g of epoxy-terminated polyether silicone oil with a molecular weight of 8000, 37.5g of ED-600, 33.75g of ED-900, and 380g of isopropanol at 80-83°C for 8 hours, and then distill at this temperature under normal pressure. At this time, A large number of fractions are distilled out, observe the distillate receiving tank, when 130g of isopropanol is evaporated, add 70g of dipropylene glycol; continue distillation at atmospheric pressure, after 260g of isopropanol is evaporated, then add 70g of dipropylene glycol, then change to decompression Distill (-0.09MPa), raise the temperature to 95°C-100°C until no fraction is distilled out, and the tot...
Embodiment 3
[0036](1) Add terminal hydrogen-containing silicone oil with a molecular weight of 12500, allyl epoxy polyether with a molecular weight of 500, and isopropanol into the reaction kettle, start stirring, and raise the temperature to 80-83°C, react for 7 hours, and obtain a molecular weight It is 13500 end epoxy polyether silicone oil. React 500g of epoxy-terminated polyether silicone oil with a molecular weight of 13500, 26.66g of ED-900, 25.9g of ED-2003, and 675g of isopropanol at 80-83°C for 18 hours, and then distill at this temperature under normal pressure. At this time, A large number of fractions are distilled out, observe the distillate receiving tank, when 225g of isopropanol is distilled out, add 115g of isohexanediol; Distill under reduced pressure (-0.08MPa), heat up to 95°C to 100°C until no fraction is distilled, and the total isopropanol in the fraction receiving tank is 675g to obtain an environmentally friendly ternary copolymerization block silicon crude oil. ...
PUM
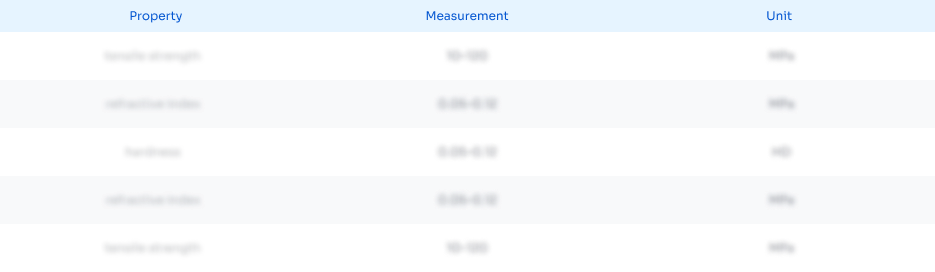
Abstract
Description
Claims
Application Information

- Generate Ideas
- Intellectual Property
- Life Sciences
- Materials
- Tech Scout
- Unparalleled Data Quality
- Higher Quality Content
- 60% Fewer Hallucinations
Browse by: Latest US Patents, China's latest patents, Technical Efficacy Thesaurus, Application Domain, Technology Topic, Popular Technical Reports.
© 2025 PatSnap. All rights reserved.Legal|Privacy policy|Modern Slavery Act Transparency Statement|Sitemap|About US| Contact US: help@patsnap.com