Alkaline ceramic grease deacidification agent preparation method
The technology of deacidification agent and ceramics, which is applied in the field of oil deacidification agent, can solve the problems of high energy consumption, complex process and environmental pollution, and achieve the effect of short processing time, simple process and no environmental pollution.
- Summary
- Abstract
- Description
- Claims
- Application Information
AI Technical Summary
Problems solved by technology
Method used
Examples
example 1
[0017] Cut a piece of soft polyurethane foam of 1cm×1cm×1cm, soak it in 100mL sodium hydroxide solution with a mass fraction of 10%, soak it in a constant temperature water bath at 60°C for 2 hours, take out the soft polyurethane foam, and wash it twice with deionized water After that, soak it in a solution of 1% sodium carboxymethylcellulose by mass fraction, soak it in a constant temperature water bath at 60°C for 1 hour, then take out the soft polyurethane foam and dry it naturally to obtain a surface pretreated soft polyurethane foam; Take 1.2g of sodium chloride, 2g of sodium silicate, add 60mL of deionized water, stir at 300r / min for 10min, then add 25g of diatomaceous earth, 7mL of 10% diethylene glycol diacrylate solution , stirred at 800r / min for 10h to obtain a diatomite slurry; after immersing the above-mentioned surface pretreated soft polyurethane foam in the above-mentioned diatomite slurry for 3min, take out the polyurethane foam and press off the excess slurry w...
example 2
[0020]Cut a piece of soft polyurethane foam of 1cm×1cm×1cm, soak it in 120mL sodium hydroxide solution with a mass fraction of 10%, soak it in a constant temperature water bath at 62°C for 2.5h, take out the soft polyurethane foam, and wash it with deionized water for 2 hours After three times, it was soaked in 1% sodium carboxymethyl cellulose solution with a mass fraction of 1.5 h in a constant temperature water bath at 62°C, and then the soft polyurethane foam was taken out and air-dried naturally to obtain a surface pretreated soft polyurethane foam. ; Weigh 1.3g sodium chloride, 3g sodium silicate, add 62mL deionized water, stir at 350r / min for 12min, then add 28g diatomaceous earth, 7.5mL mass fraction is 10% diethylene glycol diphthalate Acrylic ester solution, stirred at 900r / min for 11h to obtain diatomite slurry; after immersing the above-mentioned surface pretreated flexible polyurethane foam in the above-mentioned diatomite slurry for 4min, take out the polyurethane...
example 3
[0023] Cut a piece of soft polyurethane foam of 1cm×1cm×1cm, soak it in 150mL of 10% sodium hydroxide solution, soak it in a constant temperature water bath at 65°C for 3 hours, take out the soft polyurethane foam, and wash it three times with deionized water After that, soak it in a solution of sodium carboxymethylcellulose with a mass fraction of 1%, and soak it in a constant temperature water bath at 65°C for 2 hours, then take out the soft polyurethane foam and dry it naturally to obtain a surface pretreated soft polyurethane foam; Take 1.5g sodium chloride, 5g sodium silicate, add 65mL deionized water, stir at 400r / min for 15min, then add 30g diatomaceous earth, 8mL mass fraction is 10% diethylene glycol diacrylate solution , stirred at 1000r / min for 12h to obtain a diatomite slurry; after immersing the above-mentioned surface pretreated soft polyurethane foam in the above-mentioned diatomite slurry for 5min, take out the polyurethane foam and press off the excess slurry w...
PUM
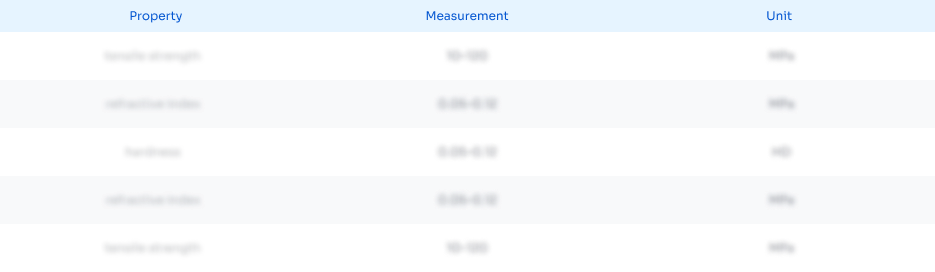
Abstract
Description
Claims
Application Information

- R&D Engineer
- R&D Manager
- IP Professional
- Industry Leading Data Capabilities
- Powerful AI technology
- Patent DNA Extraction
Browse by: Latest US Patents, China's latest patents, Technical Efficacy Thesaurus, Application Domain, Technology Topic, Popular Technical Reports.
© 2024 PatSnap. All rights reserved.Legal|Privacy policy|Modern Slavery Act Transparency Statement|Sitemap|About US| Contact US: help@patsnap.com