Preparation method for polytrimethylene terephthalate
A technology of polytrimethylene terephthalate and polytrimethylene phthalate, which is applied in the field of preparation of polytrimethylene terephthalate, can solve the problems of inactivation of titanium compounds, improve intrinsic viscosity and solve catalyst activity problems Effect
- Summary
- Abstract
- Description
- Claims
- Application Information
AI Technical Summary
Problems solved by technology
Method used
Image
Examples
Embodiment 1
[0035] Mix 142g of tetraisopropyl titanate with 46g of ethanol and 90g of lactic acid, and react for 4 hours at a temperature of 100°C in a stirred reactor. Add 36g of magnesium acetate and 91g of triethyl phosphate to the reactant. In the reactor, the reaction was carried out for 4 hours under the temperature condition of 120°C. The reaction product is placed in a reactor equipped with a fractionation device, and ethanol and isopropanol are distilled off to make a catalyst. The catalyst is mixed with 1,3-propanediol, wherein the mass fraction of titanium atoms is 4%.
[0036] 600g of terephthalic acid, 439g of 1,3 propylene glycol, 3.1g of sorbitol and 1.49g of catalyst are mixed to form a slurry, which is added to a polymerization kettle for esterification reaction. The esterification temperature is 230°C and the pressure is 0.25MPa. The rectifying device discharges the water generated by the reaction, and reacts for 2 hours. After the esterification is completed, the pres...
Embodiment 2
[0039] Mix 142g of tetraisopropyl titanate with 46g of ethanol and 192g of citric acid, and react in a stirred reactor at a temperature of 100°C for 4 hours, add 36g of magnesium acetate and 91g of triethyl phosphate to the reactant, In a stirred reactor, the reaction was carried out at a temperature of 120° C. for 4 hours. The reaction product is placed in a reactor equipped with a fractionation device, and ethanol and isopropanol are distilled off to make a catalyst. The catalyst is mixed with 1,3-propanediol, wherein the mass fraction of titanium atoms is 4%.
[0040]600g of terephthalic acid, 439g of 1,3 propylene glycol, 3.1g of sorbitol and 1.49g of catalyst are mixed to form a slurry, which is added to a polymerization kettle for esterification reaction. The esterification temperature is 230°C and the pressure is 0.25MPa. The rectifying device discharges the water generated by the reaction, and reacts for 2 hours. After the esterification is completed, the pressure is...
Embodiment 3
[0043] Mix 142g of tetraisopropyl titanate with 46g of ethanol and 192g of citric acid, and react for 4 hours at a temperature of 100°C in a stirred reactor, and add 61g of zinc lactate and 91g of triethyl phosphate to the reactant. In a stirred reactor, the reaction was carried out at a temperature of 120° C. for 4 hours. The reaction product is placed in a reactor equipped with a fractionation device, and ethanol and isopropanol are distilled off to make a catalyst. The catalyst is mixed with 1,3-propanediol, wherein the mass fraction of titanium atoms is 4%.
[0044] 600g of terephthalic acid, 439g of 1,3 propylene glycol, 3.1g of sorbitol and 1.49g of catalyst are mixed to form a slurry, which is added to a polymerization kettle for esterification reaction. The esterification temperature is 230°C and the pressure is 0.25MPa. The rectifying device discharges the water generated by the reaction, and reacts for 2 hours. After the esterification is completed, the pressure is...
PUM
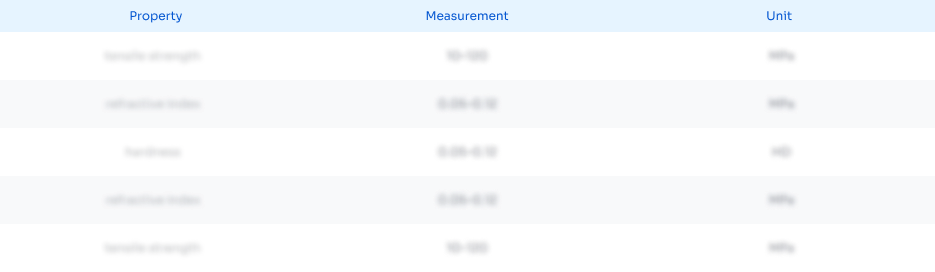
Abstract
Description
Claims
Application Information

- R&D
- Intellectual Property
- Life Sciences
- Materials
- Tech Scout
- Unparalleled Data Quality
- Higher Quality Content
- 60% Fewer Hallucinations
Browse by: Latest US Patents, China's latest patents, Technical Efficacy Thesaurus, Application Domain, Technology Topic, Popular Technical Reports.
© 2025 PatSnap. All rights reserved.Legal|Privacy policy|Modern Slavery Act Transparency Statement|Sitemap|About US| Contact US: help@patsnap.com