A self-aligning mems piezoresistive accelerometer manufacturing method
The technology of an accelerometer and its manufacturing method is applied in directions such as using inertial force for acceleration measurement, manufacturing microstructure devices, and decorative art, and can solve problems such as piezoresistor asymmetry and adverse effects on device performance, so as to improve device performance and improve The effect of device symmetry and error reduction
- Summary
- Abstract
- Description
- Claims
- Application Information
AI Technical Summary
Problems solved by technology
Method used
Image
Examples
Embodiment Construction
[0021] The invention provides a method for manufacturing a self-aligned MEMS piezoresistive accelerometer, comprising the following steps:
[0022] S1, such as figure 1 As shown, the cavity 2 is fabricated on the bottom surface of the silicon substrate 1 through a KOH etching process;
[0023] S2, combine figure 2 As shown, an oxide layer 3 with a thickness of 2000 Å and a silicon nitride layer 4 with a thickness of 2000 Å are grown sequentially from bottom to top on the top surface of the silicon substrate 1 to form a double-layer sacrificial layer;
[0024] S3, combine image 3 As shown, on the silicon nitride layer 4, the piezoresistive pattern 5 and the structure release pattern 6 are simultaneously produced by using a photolithography process, and the silicon nitride layer at the piezoresistive pattern and the structure release pattern is etched;
[0025] S4. Combination Figure 4 As shown, the oxide layer 3 at the piezoresistive pattern 5 is etched, and then the pie...
PUM
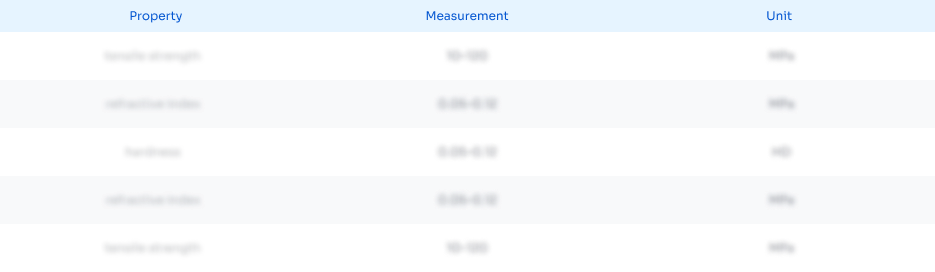
Abstract
Description
Claims
Application Information

- R&D
- Intellectual Property
- Life Sciences
- Materials
- Tech Scout
- Unparalleled Data Quality
- Higher Quality Content
- 60% Fewer Hallucinations
Browse by: Latest US Patents, China's latest patents, Technical Efficacy Thesaurus, Application Domain, Technology Topic, Popular Technical Reports.
© 2025 PatSnap. All rights reserved.Legal|Privacy policy|Modern Slavery Act Transparency Statement|Sitemap|About US| Contact US: help@patsnap.com