Earphone wire forming method
A molding method and technology for earphone cables, applied in electrical components, circuits, insulating conductors/cables, etc., can solve problems such as increased cost, inability to cover, complex manufacturing process, etc., to improve product yield and production efficiency, avoid Damage or core wire contact, the effect of reducing the difficulty of the process
- Summary
- Abstract
- Description
- Claims
- Application Information
AI Technical Summary
Problems solved by technology
Method used
Image
Examples
Embodiment Construction
[0019] In order to make the purpose, technical solutions and advantages of the invention clearer, the technical solutions in the embodiments of the present invention will be clearly and completely described below in conjunction with the accompanying drawings in the embodiments of the present invention. Obviously, the described embodiments are part of the invention Examples, not all examples. Based on the embodiments of the present invention, all other embodiments obtained by persons of ordinary skill in the art without making creative efforts belong to the protection scope of the present invention.
[0020] Such as figure 1 and figure 2 As shown, the present invention provides an embodiment of an earphone wire forming method.
[0021] The earphone cable forming method includes the following steps: performing a wire shaping step on the cut wire rod, and the wire rod shaping step includes first performing a presetting step S10 on a suitable length of the wire rod, so that the...
PUM
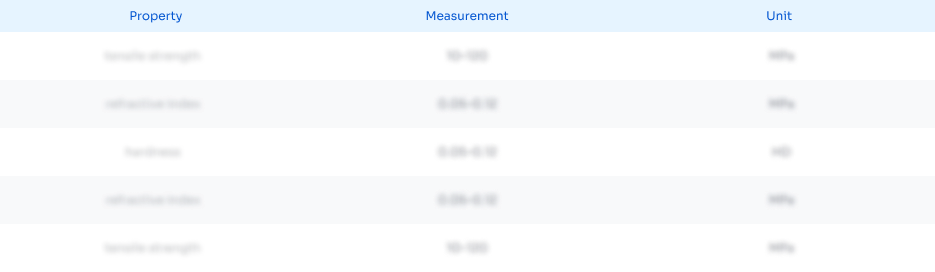
Abstract
Description
Claims
Application Information

- R&D
- Intellectual Property
- Life Sciences
- Materials
- Tech Scout
- Unparalleled Data Quality
- Higher Quality Content
- 60% Fewer Hallucinations
Browse by: Latest US Patents, China's latest patents, Technical Efficacy Thesaurus, Application Domain, Technology Topic, Popular Technical Reports.
© 2025 PatSnap. All rights reserved.Legal|Privacy policy|Modern Slavery Act Transparency Statement|Sitemap|About US| Contact US: help@patsnap.com