Insulated high-voltage optical fiber composite power cable
A fiber optic composite and power cable technology, applied in the direction of insulated cables, power cables, power cables including optical transmission components, etc., can solve the problem of increasing the outer diameter of conductors and cables, the difficulty of production organization, and increasing the contact surface and contact degree To achieve the effect of improving surface quality and electrical performance, ensuring cable bending performance, and strong external force collision function
- Summary
- Abstract
- Description
- Claims
- Application Information
AI Technical Summary
Problems solved by technology
Method used
Image
Examples
Embodiment Construction
[0016] The present invention will be further described below in conjunction with accompanying drawing.
[0017] Such as figure 1 The shown insulated high-voltage optical fiber composite power cable includes a solid aluminum conductor 1 located in the center of the cable. Outside the solid aluminum conductor, four first fan-shaped solid aluminum wires 2 of the same shape and size are extruded, and then the ring-shaped ones are extruded. The second solid aluminum-shaped wire 3; the second aluminum-shaped wire is extruded and wrapped with a low-density polyethylene insulating layer 4, and the double-layer water-blocking tape 5 is overlapped and wrapped, and the corrugated aluminum sheath 6 is welded outside the water-blocking tape. An alkali-free glass fiber tape 7 is wrapped around the sheath, and an outer sheath 8 of medium-density polyethylene is extruded on the outermost layer of the cable; an optical fiber 9 is provided in each first solid aluminum-shaped wire.
[0018] The...
PUM
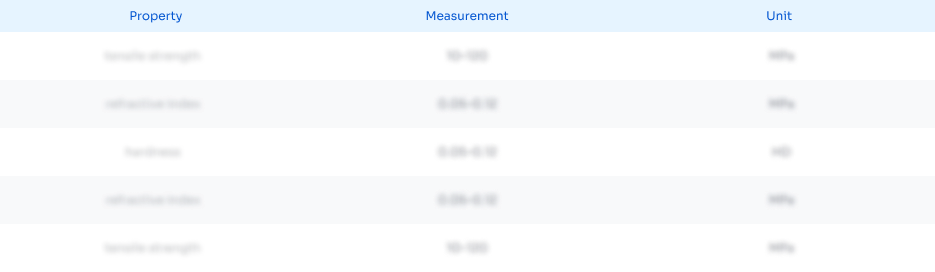
Abstract
Description
Claims
Application Information

- Generate Ideas
- Intellectual Property
- Life Sciences
- Materials
- Tech Scout
- Unparalleled Data Quality
- Higher Quality Content
- 60% Fewer Hallucinations
Browse by: Latest US Patents, China's latest patents, Technical Efficacy Thesaurus, Application Domain, Technology Topic, Popular Technical Reports.
© 2025 PatSnap. All rights reserved.Legal|Privacy policy|Modern Slavery Act Transparency Statement|Sitemap|About US| Contact US: help@patsnap.com