A preparing method for a hydrogen production composite catalytic electrode
A catalytic electrode, metal titanium technology, applied in the direction of electrodes, electrolysis process, electrolysis components, etc., can solve the problems of poor conductivity, limited edge length, insufficient number of active sites, etc., to solve the problem of easy agglomeration and regular morphology of products. , the effect of easy control of reaction conditions
- Summary
- Abstract
- Description
- Claims
- Application Information
AI Technical Summary
Problems solved by technology
Method used
Image
Examples
Embodiment 1
[0030] The titanium mesh with a geometric area of 5 square centimeters was ultrasonically cleaned with deionized water, alcohol and acetone for 30 minutes in order to remove surface organic matter. 6 mmol of CoCl 2 ·6H 2 O, 4 mmol NH 4 Cl, 3 mmol of CO(NH 2 ) 2 Dissolve in 16 mL of deionized water and stir for 20 min. The clear pink solution was then transferred into a Teflon liner (20 mL), the titanium mesh was stood in the liner, and placed in a stainless steel autoclave. The autoclave was sealed and placed in an electric oven, reacted at 120 degrees Celsius for 6 hours, and then cooled to room temperature. Take out the titanium mesh, wash it, and dry it at 70 degrees Celsius for 12 hours. Co(OH) obtained by SEM 2 The topography of / Ti is as follows figure 1 shown.
[0031] Dissolve 5 mmol of ammonium molybdate and 15 mmol of thioacetamide in 30 mL of deionized water and stir to form a transparent solution. The solution was then transferred to a Teflon liner (40 ...
Embodiment 2
[0035] A titanium sheet with a geometric area of 8 square centimeters was ultrasonically cleaned with deionized water, alcohol and acetone for 30 minutes in order to remove surface organic matter. 5 mmol of Co(NO 3 ) 2 ·6H 2 O, 5 mmol of (NH 4 ) 2 CO 3 , 4 mmol of ammonia water was dissolved in 50 ml of deionized water and stirred for 30 min. The clear pink solution was then transferred to a polytetrafluoroethylene liner (60 ml), and the titanium piece was placed in the liner and placed in a stainless steel autoclave. The autoclave was sealed and placed in an electric oven, reacted at 60 degrees Celsius for 12 hours, and then cooled to room temperature. The titanium sheet was taken out and washed, and dried at 60 degrees Celsius for 24 hours.
[0036] Dissolve 2 mmol of sodium molybdate and 10 mmol of sodium sulfide in 40 mL of deionized water and stir to form a transparent solution. The solution was then transferred to a Teflon liner (40 mL) and a 6 cm2 piece of Co(...
PUM
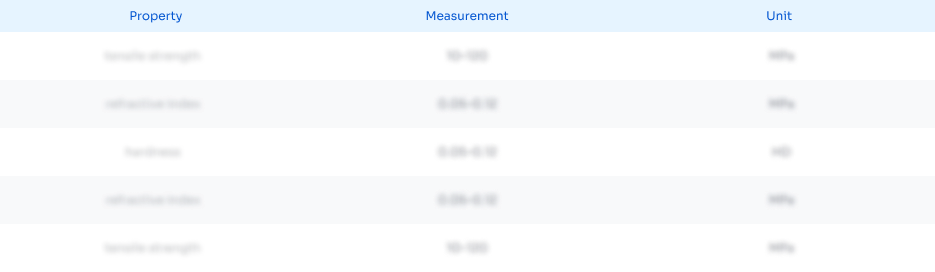
Abstract
Description
Claims
Application Information

- R&D Engineer
- R&D Manager
- IP Professional
- Industry Leading Data Capabilities
- Powerful AI technology
- Patent DNA Extraction
Browse by: Latest US Patents, China's latest patents, Technical Efficacy Thesaurus, Application Domain, Technology Topic, Popular Technical Reports.
© 2024 PatSnap. All rights reserved.Legal|Privacy policy|Modern Slavery Act Transparency Statement|Sitemap|About US| Contact US: help@patsnap.com