Method for recycling cobalt and lithium from positive plate of waste lithium ion battery
A technology for lithium ion batteries and positive electrode sheets, which is applied in the field of recovering cobalt and lithium, can solve the problems of high cost, long process flow, difficulty in improving economic benefits and industrialization value, etc., and is suitable for large-scale industrialization and has a simple and easy process. , the effect of considerable economic value
- Summary
- Abstract
- Description
- Claims
- Application Information
AI Technical Summary
Problems solved by technology
Method used
Image
Examples
Embodiment 1
[0026] Such as figure 1 As shown, the method for recovering cobalt and lithium from the positive electrode sheet of the waste lithium-ion battery provided by the present embodiment includes the following steps:
[0027] 1. Ammonium sulfate roasting process:
[0028] Mix the positive electrode sheet of the waste lithium battery with ammonium sulfate at a mass ratio of 1:2.5, and then bake at 650°C for 4 hours to obtain reduced roasted slag containing aluminum foil and sulfate containing metal elements such as cobalt and lithium;
[0029] 2. Screening process:
[0030] Using a vibrating sieving machine to sieve the reduced roasted slag while vibrating, separate and remove the aluminum foil, and obtain a reduced slag containing cobalt and lithium. The cobalt content in the reduced slag is 45.4wt.%, and the lithium content is 6.2wt.%.
[0031] 3. Acid leaching process:
[0032] Use 2mol / L dilute sulfuric acid at a liquid-solid ratio of 6:1 (L / kg) to leach the cobalt-lithium-con...
Embodiment 2
[0042] Such as figure 1 As shown, the method for recovering cobalt and lithium from the positive electrode sheet of the waste lithium-ion battery provided by the second embodiment includes the following steps:
[0043] 1. Ammonium sulfate roasting process:
[0044] Mix the positive electrode sheet of the waste lithium battery with ammonium sulfate at a mass ratio of 1:2.0, and then bake at 550°C for 7 hours to obtain reduced roasted slag containing aluminum foil and sulfate containing metal elements such as cobalt and lithium;
[0045] 2. Screening process:
[0046]The reduced roasted slag was sieved while vibrating with a vibrating sieving machine, and the aluminum foil was separated and removed to obtain a reduced slag containing cobalt and lithium. The cobalt content in the reduced slag was 48.9wt.%, and the lithium content was 7.2wt.%.
[0047] 3. Acid leaching process:
[0048] Use 1mol / L dilute sulfuric acid at a liquid-solid ratio of 8:1 (L / kg) to leach the cobalt-li...
Embodiment 3
[0058] Such as figure 1 As shown, the method for recovering cobalt and lithium from the positive electrode sheet of the waste lithium ion battery provided by the present embodiment three includes the following steps:
[0059] 1. Ammonium sulfate roasting process:
[0060] Mix the positive electrode sheet of the waste lithium battery with ammonium sulfate at a mass ratio of 1:2.2, and then bake at 550°C for 6 hours to obtain a reduced roasted slag containing aluminum foil and sulfate containing metal elements such as cobalt and lithium;
[0061] 2. Screening process:
[0062] Using a vibrating sieving machine to sieve the reduced roasted slag while vibrating, separate and remove the aluminum foil, and obtain a reduced slag containing cobalt and lithium. The cobalt content in the reduced slag is 47.3wt.%, and the lithium content is 6.8wt.%.
[0063] 3. Acid leaching process:
[0064] Use 1mol / L dilute sulfuric acid at a liquid-solid ratio of 5:1 (L / kg) to leach the cobalt-lit...
PUM
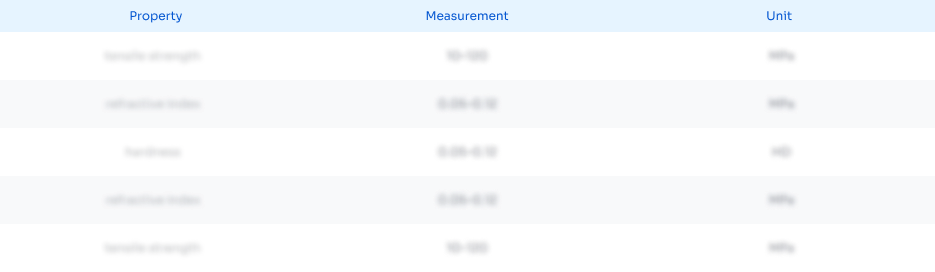
Abstract
Description
Claims
Application Information

- R&D
- Intellectual Property
- Life Sciences
- Materials
- Tech Scout
- Unparalleled Data Quality
- Higher Quality Content
- 60% Fewer Hallucinations
Browse by: Latest US Patents, China's latest patents, Technical Efficacy Thesaurus, Application Domain, Technology Topic, Popular Technical Reports.
© 2025 PatSnap. All rights reserved.Legal|Privacy policy|Modern Slavery Act Transparency Statement|Sitemap|About US| Contact US: help@patsnap.com