Stress simulation method for polycrystalline cbn abrasive grain brazing and grinding synergy based on Thiessen polygon segmentation
A Thiessen polygonal and synergistic technology, applied in design optimization/simulation, special data processing applications, instruments, etc., can solve problems such as inability to accurately analyze the stress distribution of brazing abrasive grain grinding, and achieve the effect of simplifying the calculation process
- Summary
- Abstract
- Description
- Claims
- Application Information
AI Technical Summary
Problems solved by technology
Method used
Image
Examples
Embodiment 1
[0043] The stress simulation method of polycrystalline CBN abrasive grain brazing and grinding synergy based on Thiessen polygon segmentation, the steps are as follows:
[0044] Step 1: Thiessen polygon segmentation
[0045] First, numerical calculation software (Matlab) is used to randomly distribute n points in a square area whose length and width are l; use the Thiessen polygon segmentation function (Voronoi) of Matlab software to perform Thiessen polygon segmentation on these n points, forming n microcrystalline particles. l takes 0.5mm here, and n takes 625 here.
[0046] Since polycrystalline CBN abrasive grains are composed of microcrystalline CBN particles and AlN binder, it is necessary to add AlN binder belts in the model. Such as Figure 8 Shown is the crystallite polygon after Thiessen polygon segmentation, and its vertex coordinates are (x i ,y i ), the face center coordinates are (x c ,y c ), the area of the polygon is A. Then the polygon vertex coordin...
PUM
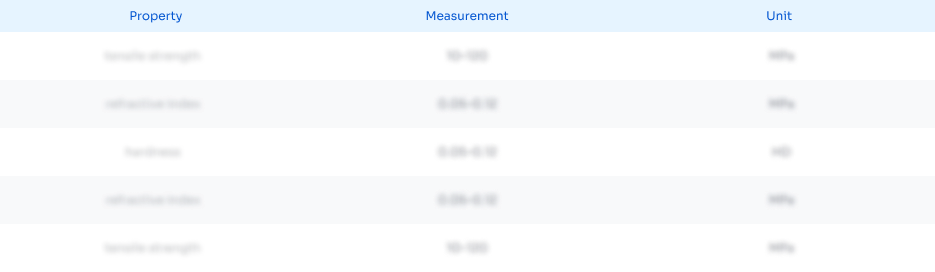
Abstract
Description
Claims
Application Information

- R&D
- Intellectual Property
- Life Sciences
- Materials
- Tech Scout
- Unparalleled Data Quality
- Higher Quality Content
- 60% Fewer Hallucinations
Browse by: Latest US Patents, China's latest patents, Technical Efficacy Thesaurus, Application Domain, Technology Topic, Popular Technical Reports.
© 2025 PatSnap. All rights reserved.Legal|Privacy policy|Modern Slavery Act Transparency Statement|Sitemap|About US| Contact US: help@patsnap.com