Coaxial electrospun polyimide micro/nano hollow structure material and preparation method thereof
A polyimide and coaxial electrospinning technology, which is applied in electrospinning, filament/thread forming, textiles and papermaking, etc., can solve the complicated preparation process, the great influence of environmental factors, and the strict control of preparation conditions, etc. problems, to achieve the effect of high yield and simple and convenient preparation process
- Summary
- Abstract
- Description
- Claims
- Application Information
AI Technical Summary
Problems solved by technology
Method used
Image
Examples
Embodiment 1
[0032] Dissolve 3 g of soluble polyimide PI (αBPDA-TFDB) in 7 g of DMF; at the same time, dissolve 2 g of polyvinylpyrrolidone PVP in 8 g of DMAc, and stir at room temperature until uniform PI solution and PVP solution. Put the PI solution in the syringe and connect it with the shell of the coaxial needle, put the PVP solution in the syringe and connect it with the core layer of the coaxial needle, as attached figure 1 As shown; at room temperature, the working voltage is 30kV, the injection speed of the shell medium is 2mL / h, the injection speed of the core medium is 1mL / h, and the receiving distance (between the Taylor cone and the aluminum foil) is 30cm, the core-shell is obtained by coaxial electrospinning structure of micro / nanofibers, the specific structure is attached figure 2 And attached image 3shown. Soak the micro / nano fibers with core-shell structure in deionized water at 50° C. for 3 hours, then take them out and dry them to obtain polyimide micro / nano hollow ...
Embodiment 2
[0034] Dissolve 2.5g of soluble polyimide PI (αBPDA-TFDB) in 7.5g of DMF; at the same time, dissolve 0.5g of PEO in 9.5g of DMAc, and stir at room temperature until uniform PI solution and PEO solution. Put the PI solution in the syringe and connect it with the shell of the coaxial needle, and put the PEO solution in the syringe and connect it with the core of the coaxial needle; the working voltage at room temperature is 10kV, and the injection speed of the shell medium is 0.5mL / h. The injection speed of the core medium was 0.1mL / h, and the receiving distance was 5cm, and the micro / nanofibers with the core-shell structure were obtained by coaxial electrospinning. Soak the micro / nano fibers with core-shell structure in deionized water at 50° C. for 3 hours, then take them out and dry them to obtain polyimide micro / nano hollow fibers.
Embodiment 3
[0036] 3 g of soluble polyimide PI (αBPDA-TFDB) was dissolved in 7 g of DMF, while 3 g of PEG was dissolved in 7 g of DMAc, and stirred at room temperature until uniform PI solution and PEG solution were obtained. Put the PI solution in the syringe and connect it with the shell layer of the coaxial needle, and put the PEG solution in the syringe and connect it with the core layer of the coaxial needle; Under the conditions of injection speed of 1mL / h and receiving distance of 30cm, micro / nanofibers with core-shell structure were obtained by coaxial electrospinning. Soak the micro / nano fibers with core-shell structure in deionized water at 50° C. for 3 hours, then take them out and dry them to obtain polyimide micro / nano hollow fibers.
PUM
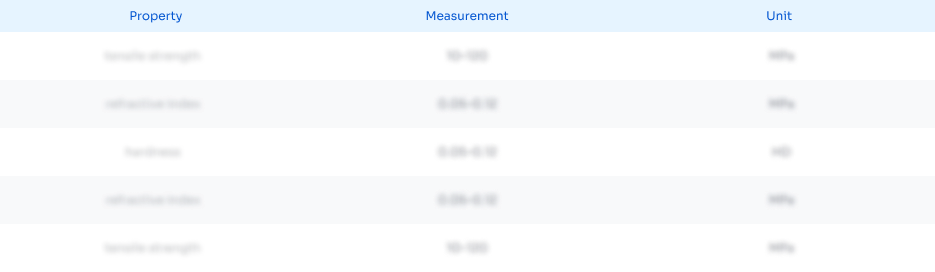
Abstract
Description
Claims
Application Information

- R&D Engineer
- R&D Manager
- IP Professional
- Industry Leading Data Capabilities
- Powerful AI technology
- Patent DNA Extraction
Browse by: Latest US Patents, China's latest patents, Technical Efficacy Thesaurus, Application Domain, Technology Topic, Popular Technical Reports.
© 2024 PatSnap. All rights reserved.Legal|Privacy policy|Modern Slavery Act Transparency Statement|Sitemap|About US| Contact US: help@patsnap.com