Reagent and method for enhancing mechanical performance of electrostatic spinning film
An electrospinning and thin film technology, which is applied in the direction of electrospinning, filament/thread forming, textiles and papermaking, etc., can solve the problem of high cost of inorganic nanomaterials such as carbon nanotubes, easy damage to fiber structure, and insignificant reinforcement effect, etc. problem, to achieve the effect of simple equipment and site requirements, simple operation process, and good enhancement effect
- Summary
- Abstract
- Description
- Claims
- Application Information
AI Technical Summary
Problems solved by technology
Method used
Image
Examples
Embodiment 1
[0020] This example demonstrates the reagent and method for enhancing the mechanical properties of electrospun films provided by the present invention by enhancing the mechanical properties of PLA electrospun films.
[0021] First: prepare polylactic acid (PLA, polylactic acid) electrospun film by electrospinning technology; second: choose chloroform as solvent and water as non-solvent; then determine the mixing ratio of chloroform and water: 1:9 to 5:5 Sprinkle a mixture of chloroform and water on the surface of the film, let it stand for 30 minutes, and wait for it to fully act, then volatilize the chloroform and water, observe the volatilized film with a scanning electron microscope, and discard the proportions that show signs of fiber dissolution , the highest value is selected as the optimal ratio for the ratio that does not dissolve; the ratio of adding chloroform and water is 4:6 in this embodiment; 10ml / cm 2 Sprinkle the reagent on the PLA electrospinning film; then c...
Embodiment 2
[0025] This example demonstrates the reagent and method for enhancing the mechanical properties of electrospun films provided by the present invention by enhancing the mechanical properties of polycarbonate (PC, Polycarbonate) electrospun films.
[0026] First: prepare PC electrospun film by electrospinning technology; secondly: select tetrahydrofuran as solvent and water as non-solvent; then determine the mixing ratio of tetrahydrofuran and water: mix 1:9 to 5:5 ratio of tetrahydrofuran and water Sprinkle the mixture on the surface of the film, let it stand for 30 minutes, and wait for its full effect, then volatilize the tetrahydrofuran and water, observe the volatilized film with a scanning electron microscope, discard the proportion that shows signs of fiber dissolution, and select the proportion that does not occur The highest value is taken as the optimal ratio; in this example, the ratio of adding tetrahydrofuran to water is 3:7; 2 Sprinkle the reagent on the PC electro...
Embodiment 3
[0030] This example demonstrates the reagent and method for enhancing the mechanical properties of electrospun films provided by the present invention by enhancing the mechanical properties of polycarbonate (PC, Polycarbonate) electrospun films. In this embodiment, a mixture of tetrahydrofuran and dimethylformamide is selected as a solvent, and a mixture of water and ethanol is used as a non-solvent; wherein the mixing ratio of tetrahydrofuran and dimethylformamide is any ratio, and the ratio selected in this embodiment is 6:4, , the mixing ratio of water and ethanol is any ratio, and the selection ratio of this embodiment is: 5:5
[0031] Determine the mixing ratio of solvent and non-solvent: pour a mixture of solvent and non-solvent in a ratio of 1:9 to 5:5 on the surface of the film, let it stand for 30 minutes, and wait for it to fully act, then volatilize the solvent and non-solvent, and then The thin film after volatilization is carried out scanning electron microscope o...
PUM
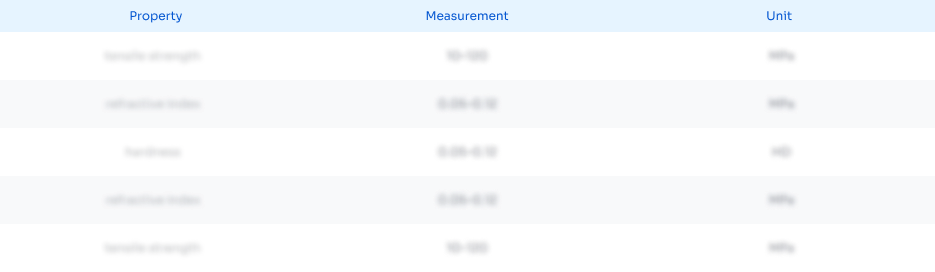
Abstract
Description
Claims
Application Information

- R&D
- Intellectual Property
- Life Sciences
- Materials
- Tech Scout
- Unparalleled Data Quality
- Higher Quality Content
- 60% Fewer Hallucinations
Browse by: Latest US Patents, China's latest patents, Technical Efficacy Thesaurus, Application Domain, Technology Topic, Popular Technical Reports.
© 2025 PatSnap. All rights reserved.Legal|Privacy policy|Modern Slavery Act Transparency Statement|Sitemap|About US| Contact US: help@patsnap.com