Bainite steel rail and preparation method thereof
A bainite and bainitic ferrite technology, applied in the field of rail materials, can solve the problems of inability to obtain stress indicators, hidden dangers of driving safety, rail bending, etc., and achieve the effects of excellent service safety and excellent toughness and toughness.
- Summary
- Abstract
- Description
- Claims
- Application Information
AI Technical Summary
Problems solved by technology
Method used
Image
Examples
preparation example Construction
[0029] According to the second aspect of the present invention, the present invention also provides a method for preparing the above-mentioned bainitic steel rail, which method includes: rolling the steel slab after heat preservation treatment to obtain a waste heat rail, and cooling the tread center of the waste heat rail in air to After the center temperature of the rail head tread is 350-370°C, temper the obtained waste heat rail at 375-405°C for 4-8h, and then cool it to room temperature in air.
[0030] According to the method of the present invention, based on the weight of the steel slab, the steel slab contains 0.20-0.30% by weight of C, 1.40-1.60% by weight of Si, 1.85-2.05% by weight of Mn, 1.00%-1.25% by weight of Cr, 0.30%-0.50% by weight of Mo, 0.07%-0.09% by weight of V, and satisfying 3.1% by weight≤Mn+Cr≤3.3% by weight.
[0031] According to the method of the present invention, the steel slab of the above composition can be obtained by conventional methods in t...
Embodiment 1-6
[0048] Examples 1-6 are used to illustrate the preparation method of the bainitic steel rail provided by the present invention.
[0049] The A1-A6 steel billets in Table 1 were cast into continuous casting billets with a certain cross-sectional size after being smelted in a converter, refined in an LF furnace, and treated in a RH vacuum. Roll the steel billet into a cross-section rail of 60kg / m, place the obtained waste heat rail upright on the roller table and let it stand in the air for air cooling. Put the rail in the tempering furnace for tempering, see Table 2 for the tempering temperature and time, then take it out and continue air cooling to room temperature.
PUM
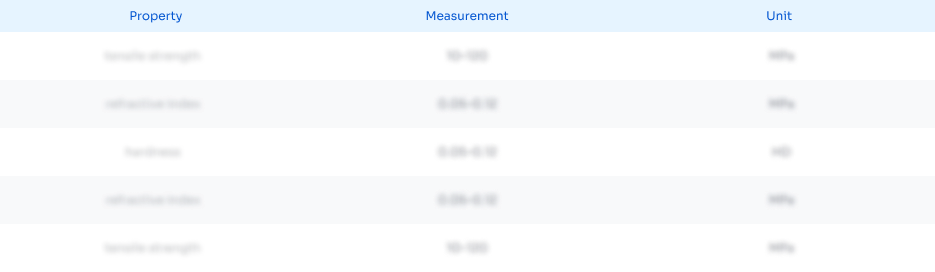
Abstract
Description
Claims
Application Information

- R&D
- Intellectual Property
- Life Sciences
- Materials
- Tech Scout
- Unparalleled Data Quality
- Higher Quality Content
- 60% Fewer Hallucinations
Browse by: Latest US Patents, China's latest patents, Technical Efficacy Thesaurus, Application Domain, Technology Topic, Popular Technical Reports.
© 2025 PatSnap. All rights reserved.Legal|Privacy policy|Modern Slavery Act Transparency Statement|Sitemap|About US| Contact US: help@patsnap.com