Modified thin oil lubrication drum-shaped tooth type coupling
A thin oil lubrication, drum-shaped tooth technology, used in engine lubrication, driving devices for metal rolling mills, metal rolling, etc. Improve the overall service life, ensure the overall service life, and improve the effect of sealing reliability
- Summary
- Abstract
- Description
- Claims
- Application Information
AI Technical Summary
Problems solved by technology
Method used
Image
Examples
Embodiment 1
[0087] The present invention is an adjustable thin oil lubricated drum gear coupling, which includes a main shaft 13, a roller end assembly E, a gear end assembly F, an oil inlet ring assembly H, a spring assembly 15, and a roller end assembly E 1. The tooth end assembly F and the oil inlet ring assembly H are arranged on the main shaft 13, the spring assembly 15 is arranged in the main shaft 13, and the roller end assembly E is an adjustable roller end assembly, which includes a roller end bushing, a roller end connection plate 8, Outer centering 1, inner centering 7, roll end jacking block 102, roll end outer ring gear 107, roll end connecting disc 8 and outer centering 1 are all connected to the roll end bushing, inner centering 7 and roll end jacking block 102 are all Connected with the roller end connection plate 8, the roller end bushing meshes with the roller end outer ring gear 107 through internal teeth, and the roller end outer ring gear 107 cooperates with the main s...
Embodiment 2
[0089] The roller-end bushing is a split-type roller-end bushing, which includes a roller-end bushing body 2 and two lining plates 4, and the two lining plates 4 are symmetrically arranged in the flat groove of the inner hole of the roller-end bushing body 2 Inside, the two are bonded by an inclined surface; the lining plate 4 is fastened in the flat groove of the inner hole of the roller end sleeve body 2 through the pressure plate 3, the hinge bolt 20, the elastic washer 21 and the nut 22.
[0090] In this way, by loosening the fastener and the pressing plate, the lining plate moves along the inclined plane, and the size of the dimension B between the two lining plates can be changed, so that it is suitable for occasions where the connection size is restored after wear and the connection size is different.
Embodiment 3
[0092]The outer centering 1 described above is an expansion-contraction type external centering, and the outer circle of the expansion-contraction type outer centering 1 cooperates with the left notch of the roller end sleeve body 2 through a tapered surface, and is fastened on the Inside the left seam of the roller end bushing body 2.
[0093] In this way, the inner circle diameter φD of the outer centering 1 can be changed by moving the outer centering on the tapered surface and tightening (loosening) the screw 19, so that it is suitable for restoring the connection size and different connection sizes after wear.
PUM
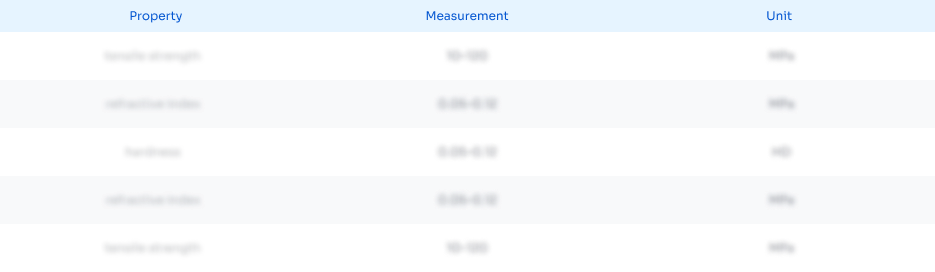
Abstract
Description
Claims
Application Information

- R&D
- Intellectual Property
- Life Sciences
- Materials
- Tech Scout
- Unparalleled Data Quality
- Higher Quality Content
- 60% Fewer Hallucinations
Browse by: Latest US Patents, China's latest patents, Technical Efficacy Thesaurus, Application Domain, Technology Topic, Popular Technical Reports.
© 2025 PatSnap. All rights reserved.Legal|Privacy policy|Modern Slavery Act Transparency Statement|Sitemap|About US| Contact US: help@patsnap.com