Continuous casting roller and assembling method thereof
A technology of continuous casting rolls and roll sleeves, applied in the field of continuous casting rolls and their assembly, can solve the problem of scrapping of mandrels and bearing assemblies, lip seals stuck in spiral grooves and/or undercut grooves, and complicated assembly. and other problems, to achieve the effect of reducing thermal fatigue load, easy interchange and maintenance, and reliable sealing performance
- Summary
- Abstract
- Description
- Claims
- Application Information
AI Technical Summary
Problems solved by technology
Method used
Image
Examples
Embodiment Construction
[0037] Such as figure 1 The continuous casting roll shown includes at least two splicing assemblies 10. This embodiment is formed by splicing three splicing assemblies 10. Each splicing assembly 10 includes a roll sleeve 11, a mandrel 12, and a bearing assembly 19. For each Parts and the relationship between the parts are described in detail:
[0038] Such as Figure 1 to Figure 3 , The roller sleeve 11 is a conventional structure, the outer peripheral surface of the roller sleeve 11 is formed by surfacing welding, and can be repaired by surfacing welding after wear and tear, so as to facilitate repeated use.
[0039] Such as Figure 1 to Figure 3 One end of the mandrel 12 is provided with a first axial blind hole 13 and a first radial hole 14 matched with the first axial blind hole 13, and the other end of the mandrel 12 is provided with a second axial blind hole 15 and a The second radial hole 16 matched with the second axial blind hole 15, the outer peripheral surface of...
PUM
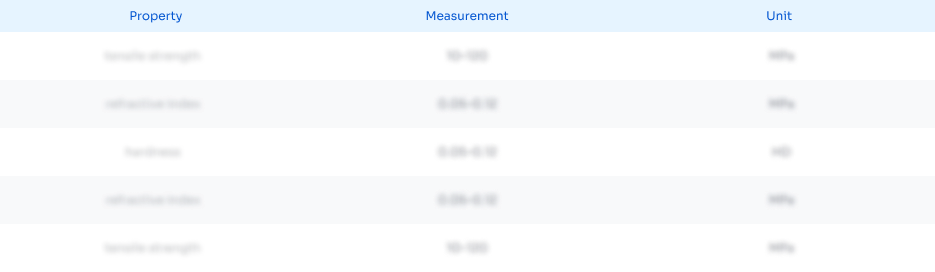
Abstract
Description
Claims
Application Information

- R&D Engineer
- R&D Manager
- IP Professional
- Industry Leading Data Capabilities
- Powerful AI technology
- Patent DNA Extraction
Browse by: Latest US Patents, China's latest patents, Technical Efficacy Thesaurus, Application Domain, Technology Topic, Popular Technical Reports.
© 2024 PatSnap. All rights reserved.Legal|Privacy policy|Modern Slavery Act Transparency Statement|Sitemap|About US| Contact US: help@patsnap.com