Heat treatment method for machining deformation prevention of 7055 aluminium alloy thin-walled structure
A heat treatment method and thin-walled structure technology, which is applied in the field of aviation material processing, can solve the problems of large residual stress, cracking and scrapping of components, and low processing accuracy, and achieve the effect of improving dimensional accuracy and preventing processing deformation
- Summary
- Abstract
- Description
- Claims
- Application Information
AI Technical Summary
Problems solved by technology
Method used
Image
Examples
Embodiment 1
[0053] Embodiment 1: The 7055 aluminum alloy forging blank is roughly machined to a sufficient margin, and after T74 heat treatment, three times of machining and three stages of aging treatment are carried out, and the steps are as follows:
[0054] a. After T74 treatment, the components are rough-machined to a certain margin of 5mm, and then undergo primary aging treatment. Temperature: 180°C, keep warm for 30 hours.
[0055] b. After the primary aging, the component is reprocessed to a certain margin of 1mm, and then the secondary aging treatment is carried out. Temperature: 200°C, keep warm for 28 hours.
[0056] c. After the secondary aging, the component is reprocessed to a certain margin of 0.5mm, and then the tertiary aging treatment is carried out. Temperature: 150°C, keep warm for 25 hours.
[0057] d. After the three-stage aging, the components are subjected to multiple finishing processes 3 times to the finished product.
Embodiment 2
[0058] Embodiment 2: The 7055 aluminum alloy forging blank is roughly machined to a sufficient margin, and after T74 heat treatment, three times of machining and three stages of aging treatment are carried out, and the steps are as follows:
[0059] a. After T74 treatment, the component is rough machined to a certain margin of 8mm, and then the primary aging treatment is performed. Temperature: 200°C, keep warm for 30 hours.
[0060] b. After the primary aging, the component is reprocessed to a certain margin of 3mm, and then the secondary aging treatment is carried out. Temperature: 190°C, keep warm for 28 hours.
[0061] c. After the secondary aging, the component is reprocessed to a certain margin of 1mm, and then the tertiary aging treatment is carried out. Temperature: 170°C, keep warm for 25 hours.
[0062] d. After the three-stage aging, the components are subjected to multiple finishing processes 3 times to the finished product.
Embodiment 3
[0063]Embodiment 3: The 7055 aluminum alloy forging blank is roughly machined to a sufficient margin. After T74 heat treatment, three times of machining and three stages of aging treatment are carried out. The steps are as follows:
[0064] a. After T74 treatment, the component is rough-machined to a certain margin of 6mm, and then undergoes primary aging treatment. Temperature: 180°C, keep warm for 30 hours.
[0065] b. After the primary aging, the component is reprocessed to a certain margin of 2mm, and then the secondary aging treatment is carried out. Temperature: 200°C, keep warm for 28 hours.
[0066] c. After the secondary aging, the component is reprocessed to a certain margin of 0.8mm, and then the tertiary aging treatment is carried out. Temperature: 150°C, keep warm for 25 hours.
[0067] d. After the three-stage aging, the components are subjected to multiple finishing processes 5 times to the finished product.
PUM
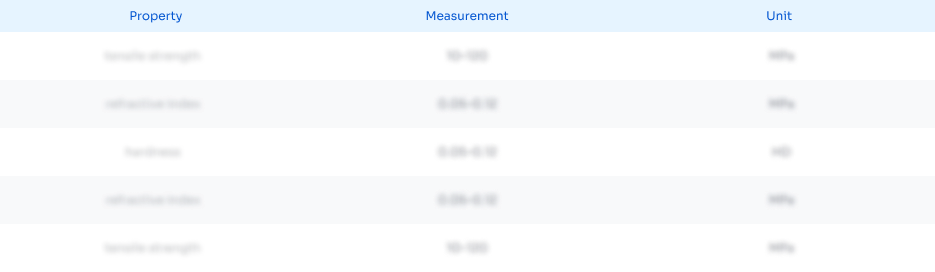
Abstract
Description
Claims
Application Information

- R&D Engineer
- R&D Manager
- IP Professional
- Industry Leading Data Capabilities
- Powerful AI technology
- Patent DNA Extraction
Browse by: Latest US Patents, China's latest patents, Technical Efficacy Thesaurus, Application Domain, Technology Topic, Popular Technical Reports.
© 2024 PatSnap. All rights reserved.Legal|Privacy policy|Modern Slavery Act Transparency Statement|Sitemap|About US| Contact US: help@patsnap.com