A preparation method of slow-release magnesium alloy for molten steel magnesium treatment
A magnesium alloy and alloy technology, applied in the field of preparation of slow-release magnesium alloys for molten steel magnesium treatment, can solve secondary oxidation and other problems, and achieve the effects of slow release, good dilution function, and increased density
- Summary
- Abstract
- Description
- Claims
- Application Information
AI Technical Summary
Problems solved by technology
Method used
Image
Examples
Embodiment 1
[0048] A kind of preparation method of slow-release magnesium alloy for molten steel magnesium treatment, adopts two-step method to prepare Mg-Al-Fe alloy, specifically as follows:
[0049] Step 1, Mg-Al alloy preparation:
[0050] (1) Raw material selection and batching calculation: according to the alloy composition ratio of Mg-Al, weigh 75kg metal Al block and 79kg metal Mg block; wherein, the mass percentage of Mg-Al alloy composition is: Mg: 50%, the balance Al and unavoidable impurities; the actual usage of metal Mg is 105% of the theoretical mass;
[0052] Using a vacuum induction furnace, after cutting metal Mg and metal Al into blocks, place the metal Mg block on the bottom of the graphite crucible, and the metal Al block is pressed on top of the metal Mg;
[0053] Raise the temperature of the vacuum induction furnace to 950°C, and evacuate during the heating process. When the vacuum degree is less than or equal to 0.01 atm, fill it with...
Embodiment 2
[0067] A kind of preparation method of slow-release magnesium alloy for molten steel magnesium treatment, adopts two-step method to prepare Mg-Al-Fe alloy, specifically as follows:
[0068] Step 1, Mg-Al alloy preparation:
[0069] (1) Raw material selection and batching calculation: according to the alloy composition ratio of Mg-Al, weigh 45kg metal Al block and 11kg metal Mg block; wherein, the mass percentage of Mg-Al alloy composition is: Mg: 70%, the balance Al and unavoidable impurities;; The mass of metal Mg is 105% of the theoretical mass;
[0071] Using a vacuum induction furnace, after cutting metal Mg and metal Al into blocks, place the metal Mg block on the bottom of the graphite crucible, and the metal Al block is pressed on top of the metal Mg;
[0072] Raise the temperature of the vacuum induction furnace to 950°C, and evacuate during the heating process. When the vacuum degree is less than or equal to 0.01 atm, fill it with Ar gas...
Embodiment 3
[0086] A kind of preparation method of slow-release magnesium alloy for molten steel magnesium treatment, adopts two-step method to prepare Mg-Al-Fe alloy, specifically as follows:
[0087] Step 1, Mg-Al alloy preparation:
[0088] (1) Raw material selection and batching calculation: according to the alloy composition ratio of Mg-Al, weigh 60kg metal Al block and 95kg metal Mg block; wherein, the mass percentage of Mg-Al alloy composition is: Mg: 60%, the balance Al and unavoidable impurities;; The mass of metal Mg is 105% of the theoretical mass;
[0090] Using a vacuum induction furnace, after cutting metal Mg and metal Al into blocks, place the metal Mg block on the bottom of the graphite crucible, and the metal Al block is pressed on top of the metal Mg;
[0091] Raise the temperature of the vacuum induction furnace to 950-1000°C, evacuate during the heating process, and when the vacuum degree is less than or equal to 0.01 atm, fill it with A...
PUM
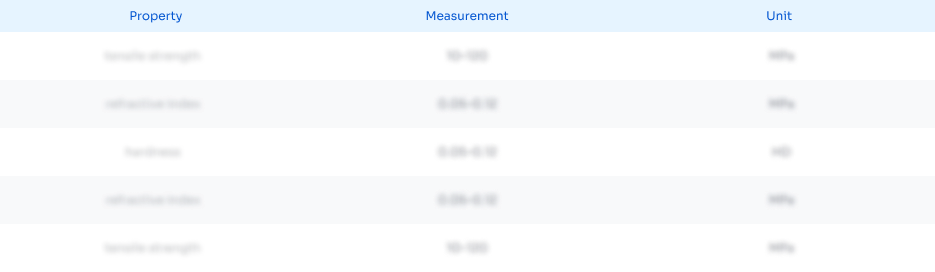
Abstract
Description
Claims
Application Information

- Generate Ideas
- Intellectual Property
- Life Sciences
- Materials
- Tech Scout
- Unparalleled Data Quality
- Higher Quality Content
- 60% Fewer Hallucinations
Browse by: Latest US Patents, China's latest patents, Technical Efficacy Thesaurus, Application Domain, Technology Topic, Popular Technical Reports.
© 2025 PatSnap. All rights reserved.Legal|Privacy policy|Modern Slavery Act Transparency Statement|Sitemap|About US| Contact US: help@patsnap.com