A kind of preparation method of antistatic filter material
A filter material and antistatic technology, which is applied in the field of preparation of antistatic filter materials, can solve the problems of filter materials such as antistatic effect and poor durability, and achieve high-efficiency and long-lasting antistatic performance, high filtration efficiency, and fiber protection effects
- Summary
- Abstract
- Description
- Claims
- Application Information
AI Technical Summary
Problems solved by technology
Method used
Image
Examples
Embodiment 1
[0053] An antistatic filter material, prepared by the following method:
[0054] S10 depositing a first conductive layer on the base cloth layer 1 . The base fabric layer 1 is made by twisting polyimide fiber filaments and carbon fibers according to a mass ratio of 2.5:1, and weaving through warp and weft phases. This step specifically includes:
[0055] Modification of the base cloth layer 1: Pretreatment of the base cloth layer 1 by pulsed atmospheric pressure air plasma, the processing power is 400W, the distance between the base cloth layer 1 and the substrate is 3cm, and the treatment time is 2min; the pretreatment The finished base cloth layer 1 was immersed in a cationic modifier solution with a temperature of 100° C. and a pH value of 9 for 25 minutes, and then padding was performed to obtain a modified base cloth layer 1 . The cationic modifier is a nitrogen heterocyclic cationic compound.
[0056] Deposit graphene quantum dots on the surface of the modified base c...
Embodiment 2
[0062] An antistatic filter material, prepared by the following method:
[0063] S10 depositing a first conductive layer on the base cloth layer 1 . The base fabric layer 1 is made by twisting polyimide fiber filaments and carbon fibers according to a mass ratio of 2:1, and weaving through warp and weft phases. This step specifically includes:
[0064] Modification of the base cloth layer 1: pretreatment of the base cloth layer 1 by pulsed atmospheric pressure air plasma, the processing power is 100W, the distance between the base cloth layer 1 and the substrate is 1cm, and the treatment time is 3min; the pretreatment The finished base fabric layer 1 was immersed in a cationic modifier solution with a temperature of 60° C. and a pH value of 8 for 30 minutes, and then padding to obtain the modified base fabric layer 1 . The cationic modifier is an epoxy compound.
[0065] Graphene quantum dots are deposited on the surface of the modified base cloth layer 1 as the first condu...
Embodiment 3
[0071] An antistatic filter material is prepared by the following method:
[0072] S10 depositing a first conductive layer on the base cloth layer 1 . The base fabric layer 1 is made by twisting polyimide fiber filaments and metal fibers according to a mass ratio of 1:1, and weaving through warp and weft phases. This step specifically includes:
[0073] Modification of the base cloth layer 1: pretreatment of the base cloth layer 1 by pulsed atmospheric pressure air plasma, the processing power is 300W, the distance between the base cloth layer 1 and the substrate is 6cm, and the treatment time is 5min; the pretreatment The finished base fabric layer 1 was immersed in a cationic modifier solution with a temperature of 80° C. and a pH value of 11 for 5 minutes, and then padding to obtain the modified base fabric layer 1 . The cationic modifier is a nitrogen heterocyclic cationic compound.
[0074] Graphene quantum dots are deposited on the surface of the modified base cloth l...
PUM
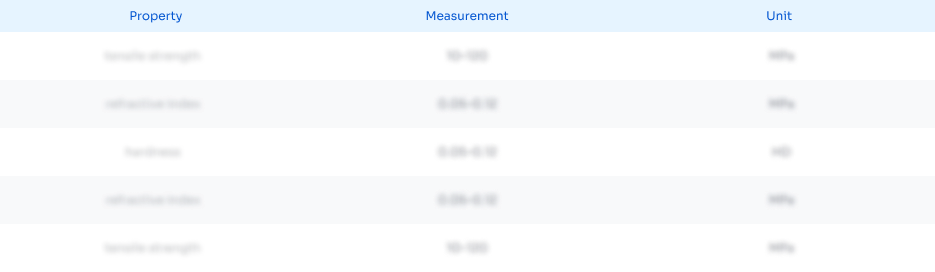
Abstract
Description
Claims
Application Information

- R&D Engineer
- R&D Manager
- IP Professional
- Industry Leading Data Capabilities
- Powerful AI technology
- Patent DNA Extraction
Browse by: Latest US Patents, China's latest patents, Technical Efficacy Thesaurus, Application Domain, Technology Topic, Popular Technical Reports.
© 2024 PatSnap. All rights reserved.Legal|Privacy policy|Modern Slavery Act Transparency Statement|Sitemap|About US| Contact US: help@patsnap.com