Preparation method of antistatic filter material
A filter material and antistatic technology, applied in the manufacture of conductive/antistatic filaments, filtration separation, membrane filters, etc. The effect of heat resistance and large specific surface area
- Summary
- Abstract
- Description
- Claims
- Application Information
AI Technical Summary
Problems solved by technology
Method used
Image
Examples
Embodiment 1
[0053] An antistatic filter material, prepared by the following method:
[0054] S10 depositing a first conductive layer on the base cloth layer 1 . The base fabric layer 1 is made by twisting polyimide fiber filaments and carbon fibers according to a mass ratio of 2.5:1, and weaving through warp and weft phases. This step specifically includes:
[0055] Modification of the base cloth layer 1: Pretreatment of the base cloth layer 1 by pulsed atmospheric pressure air plasma, the processing power is 400W, the distance between the base cloth layer 1 and the substrate is 3cm, and the treatment time is 2min; the pretreatment The finished base cloth layer 1 was immersed in a cationic modifier solution with a temperature of 100° C. and a pH value of 9 for 25 minutes, and then padding was performed to obtain a modified base cloth layer 1 . The cationic modifier is a nitrogen heterocyclic cationic compound.
[0056] Deposit graphene quantum dots on the surface of the modified base c...
Embodiment 2
[0062] An antistatic filter material, prepared by the following method:
[0063] S10 depositing a first conductive layer on the base cloth layer 1 . The base fabric layer 1 is made by twisting polyimide fiber filaments and carbon fibers according to a mass ratio of 2:1, and weaving through warp and weft phases. This step specifically includes:
[0064] Modification of the base cloth layer 1: pretreatment of the base cloth layer 1 by pulsed atmospheric pressure air plasma, the processing power is 100W, the distance between the base cloth layer 1 and the substrate is 1cm, and the treatment time is 3min; the pretreatment The finished base fabric layer 1 was immersed in a cationic modifier solution with a temperature of 60° C. and a pH value of 8 for 30 minutes, and then padding to obtain the modified base fabric layer 1 . The cationic modifier is an epoxy compound.
[0065] Graphene quantum dots are deposited on the surface of the modified base cloth layer 1 as the first condu...
Embodiment 3
[0071] An antistatic filter material is prepared by the following method:
[0072] S10 depositing a first conductive layer on the base cloth layer 1 . The base fabric layer 1 is made by twisting polyimide fiber filaments and metal fibers according to a mass ratio of 1:1, and weaving through warp and weft phases. This step specifically includes:
[0073] Modification of the base cloth layer 1: pretreatment of the base cloth layer 1 by pulsed atmospheric pressure air plasma, the processing power is 300W, the distance between the base cloth layer 1 and the substrate is 6cm, and the treatment time is 5min; the pretreatment The finished base fabric layer 1 was immersed in a cationic modifier solution with a temperature of 80° C. and a pH value of 11 for 5 minutes, and then padding to obtain the modified base fabric layer 1 . The cationic modifier is a nitrogen heterocyclic cationic compound.
[0074] Graphene quantum dots are deposited on the surface of the modified base cloth l...
PUM
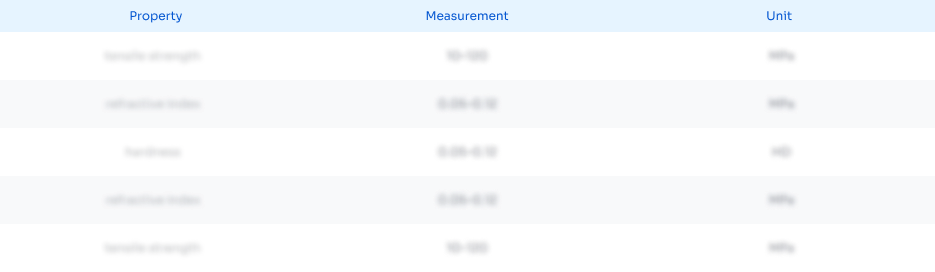
Abstract
Description
Claims
Application Information

- R&D
- Intellectual Property
- Life Sciences
- Materials
- Tech Scout
- Unparalleled Data Quality
- Higher Quality Content
- 60% Fewer Hallucinations
Browse by: Latest US Patents, China's latest patents, Technical Efficacy Thesaurus, Application Domain, Technology Topic, Popular Technical Reports.
© 2025 PatSnap. All rights reserved.Legal|Privacy policy|Modern Slavery Act Transparency Statement|Sitemap|About US| Contact US: help@patsnap.com