Antiwear agent and preparation method thereof
An anti-wear agent, lignin acid technology, applied in the field of anti-wear agent, can solve the problems of different susceptibility, unstable use effect, reduce the anti-wear performance of diesel oil, etc., and achieve good anti-wear performance, strong adaptability and superior performance. Effect
- Summary
- Abstract
- Description
- Claims
- Application Information
AI Technical Summary
Problems solved by technology
Method used
Examples
Embodiment 1
[0028] An antiwear agent is made from the following raw materials: lignin acid 18.5kg; stearic acid 19.5kg; glass glue oil 38.5kg (glass glue 25.025kg and 13.475kg industrial white oil) and pentaerythritol 21.5kg.
[0029] The preparation method comprises the following steps:
[0030] (1) glass glue and industrial white oil are compounded and mixed to form glass glue oil, and lignin acid, stearic acid, glass glue oil and pentaerythritol are mixed evenly by weight to obtain a mixed solution;
[0031] (2) Heating the mixed solution until the reaction is completed, the reaction time is 5-6 hours, and then dehydrating. After dehydration, the water content is detected as traces, and finally cooled to 90°C to obtain an intermediate product;
[0032] (3) Add 15% heavy aromatic hydrocarbons of the weight of the intermediate product to the intermediate product, keep stirring, and cool to room temperature to obtain the finished antiwear agent.
Embodiment 2
[0034] An antiwear agent made from the following raw materials:
[0035] 21.5kg of lignin acid; 20.5kg of stearic acid; 41.5kg of glass glue oil (26.975kg of glass glue and 14.525kg of industrial white oil) and 18.5kg of pentaerythritol.
[0036] The preparation method comprises the following steps:
[0037] (1) Glass glue and industrial white oil are compounded and mixed to form glass glue oil, lignin acid, stearic acid and glass glue oil are mixed for the first time according to the weight ratio, and then mixed with pentaerythritol for the second time Mix for the first time, and obtain a mixed solution after mixing evenly;
[0038] (2) Heating the mixed solution at a temperature of 120°C until the reaction is complete. The reaction time is 6 hours, and then dehydrated to a moisture content of 0.03%. After dehydration, the water content is detected as a trace, and finally cooled to 80 °C, the intermediate product was obtained;
[0039] (3) Add 15% heavy aromatic hydrocarbo...
Embodiment 3
[0041] An antiwear agent made from the following raw materials:
[0042] 20kg of lignin acid; 20kg of stearic acid; 40kg of glass glue oil (26kg of glass glue and 14kg of industrial white oil) and 20kg of pentaerythritol.
[0043] The preparation method comprises the following steps:
[0044] (1) Glass glue and industrial white oil are compounded and mixed to form glass glue oil, lignin acid, stearic acid and glass glue oil are mixed for the first time according to the weight ratio, and then mixed with pentaerythritol for the second time Mix for the first time, and obtain a mixed solution after mixing evenly;
[0045] (2) Heating the mixed solution at a temperature of 130°C until the reaction is complete. The reaction time is 5 hours, and then dehydrated to a moisture content of 0.02%. After dehydration, the water content is detected as traces, and finally cooled to 85 °C, the intermediate product was obtained;
[0046] (3) Add 15% heavy aromatic hydrocarbons of the weight ...
PUM
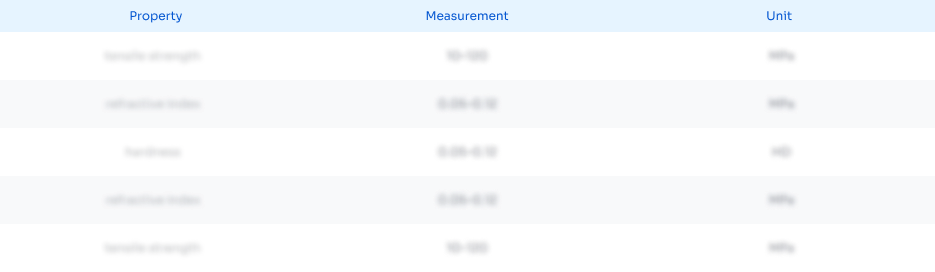
Abstract
Description
Claims
Application Information

- R&D
- Intellectual Property
- Life Sciences
- Materials
- Tech Scout
- Unparalleled Data Quality
- Higher Quality Content
- 60% Fewer Hallucinations
Browse by: Latest US Patents, China's latest patents, Technical Efficacy Thesaurus, Application Domain, Technology Topic, Popular Technical Reports.
© 2025 PatSnap. All rights reserved.Legal|Privacy policy|Modern Slavery Act Transparency Statement|Sitemap|About US| Contact US: help@patsnap.com