High-precision grating positioning device directly driven by a limited angle motor
A technology of limited rotation angle and positioning device, which is applied in the field of testing, can solve the problems of easy wear of stepping motors, compact motors, and limited service life of the system, so as to eliminate transmission errors and transmission losses, reduce development and maintenance costs, The effect of strong practicality and versatility
- Summary
- Abstract
- Description
- Claims
- Application Information
AI Technical Summary
Problems solved by technology
Method used
Image
Examples
Embodiment Construction
[0037] The following will clearly and completely describe the technical solutions in the embodiments of the present invention with reference to the accompanying drawings in the embodiments of the present invention. Obviously, the described embodiments are only some, not all, embodiments of the present invention. Based on the embodiments of the present invention, all other embodiments obtained by persons of ordinary skill in the art without making creative efforts belong to the protection scope of the present invention.
[0038] At present, in order to realize a high-precision grating rotary positioning system, the common method is to use a precision stepping motor, a high-precision harmonic reducer and an angle sensor to form a position open-loop or semi-closed-loop indirect drive control, but this method is difficult to achieve high-precision speed control , The performance requirements of the motor and the angle sensor are high, so the cost of development and maintenance is h...
PUM
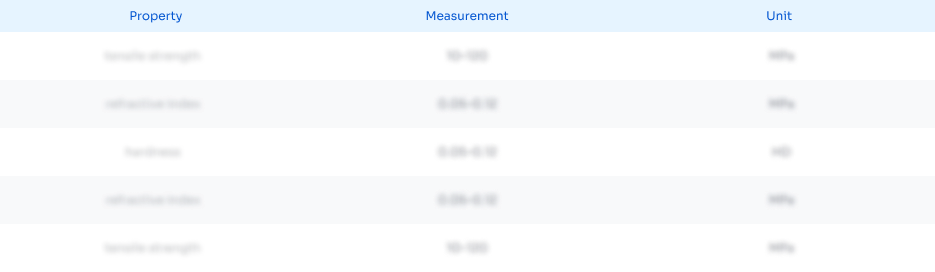
Abstract
Description
Claims
Application Information

- Generate Ideas
- Intellectual Property
- Life Sciences
- Materials
- Tech Scout
- Unparalleled Data Quality
- Higher Quality Content
- 60% Fewer Hallucinations
Browse by: Latest US Patents, China's latest patents, Technical Efficacy Thesaurus, Application Domain, Technology Topic, Popular Technical Reports.
© 2025 PatSnap. All rights reserved.Legal|Privacy policy|Modern Slavery Act Transparency Statement|Sitemap|About US| Contact US: help@patsnap.com