Method for preparing biomass synthesis gas low in nitric oxide content by mixed gasification of biomass and sludge
A low nitrogen oxide, biomass technology, applied in chemical instruments and methods, gasification process, sludge treatment and other directions, can solve the problems of difficult energy utilization of sludge, high nitrogen oxide content, and achieve reduction Effects of utilization, reduction of nitrogen oxide emissions, high application value and development prospects
- Summary
- Abstract
- Description
- Claims
- Application Information
AI Technical Summary
Problems solved by technology
Method used
Image
Examples
Embodiment 1
[0023] (1) Weigh 150 mg of pretreated dried sludge and 50 mg of corn stalks, and mix them thoroughly.
[0024] (2) Put the mixed fuel in the combustion boat, then place the combustion boat in the constant temperature section of the tube furnace, program the temperature rise, set the heating rate from room temperature to 800°C at a rate of 15°C / min, and keep it at 800°C for 30 minutes .
[0025] (3) A mixture of carbon dioxide and argon is introduced at a flow rate of 400 mL / min during the entire temperature rise process, wherein carbon dioxide accounts for 5% of the volume content.
[0026] (4) Use a flue gas analyzer to measure the content of nitric oxide in the product in real time, and integrate the content of nitric oxide to the whole process after the gasification process to obtain the total emission of nitric oxide.
[0027] (5) Collect the gas produced after the analysis by the flue gas analyzer with an air bag, and then use the GC analyzer to analyze the components of...
Embodiment 2
[0032] Step (1) is identical with embodiment 1.
[0033] (2) Put the mixed fuel in the combustion boat, then place the combustion boat in the constant temperature section of the tube furnace, program the temperature rise, set the heating rate from room temperature to 700°C at a rate of 15°C / min, and keep it at 700°C for 30 minutes .
[0034] (3) A mixture of oxygen and argon is introduced at a flow rate of 400 mL / min during the entire temperature rise process, wherein the oxygen accounts for 5% of the volume content.
[0035] Steps (4), (5) are the same as in Example 1.
[0036] (6) Compare the actual total discharge of nitric oxide measured by the experiment with the value obtained by weighting and summing the discharge of nitrogen monoxide from sludge and biomass separate gasification obtained under the same conditions, and the results show that , the emission of nitric oxide is 13% lower than that of biomass and sludge gasification alone.
[0037] At the same time, accor...
Embodiment 3
[0040] Step (1) is identical with embodiment 1.
[0041] (2) Put the mixed fuel in the combustion boat, then place the combustion boat in the constant temperature section of the tube furnace, program the temperature rise, the heating rate decreases, set the heating rate from room temperature to 800°C at 10°C / min, and Hold at 800°C for 30 minutes.
[0042] (3) A mixture of carbon dioxide and argon is introduced at a flow rate of 400 mL / min during the entire temperature rise process, wherein carbon dioxide accounts for 5% of the volume content.
[0043] Steps (4)~(5) are identical with embodiment 1
[0044] (6) Compare the actual total discharge of nitric oxide measured by the experiment with the value obtained by weighting and summing the discharge of nitrogen monoxide from sludge and biomass separate gasification obtained under the same conditions, and the results show that , the emission of nitric oxide is 9% lower than that of biomass and sludge gasification alone.
[004...
PUM
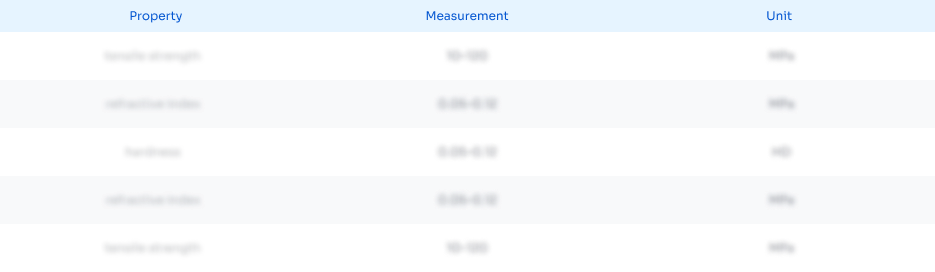
Abstract
Description
Claims
Application Information

- R&D
- Intellectual Property
- Life Sciences
- Materials
- Tech Scout
- Unparalleled Data Quality
- Higher Quality Content
- 60% Fewer Hallucinations
Browse by: Latest US Patents, China's latest patents, Technical Efficacy Thesaurus, Application Domain, Technology Topic, Popular Technical Reports.
© 2025 PatSnap. All rights reserved.Legal|Privacy policy|Modern Slavery Act Transparency Statement|Sitemap|About US| Contact US: help@patsnap.com