High-temperature wear-resistant alloy guide roll of finishing mill and preparation method thereof
A technology of high-temperature wear-resistant alloy and finishing mill, which is applied in the direction of rolls, metal rolling, metal rolling, etc., can solve the problems of low service life, poor high-temperature wear resistance, short service life of guide rolls, etc., and achieve high wear resistance performance, improve high temperature resistance, and protect the service life
- Summary
- Abstract
- Description
- Claims
- Application Information
AI Technical Summary
Problems solved by technology
Method used
Image
Examples
Embodiment 1
[0023] A high-temperature wear-resistant alloy guide roll for a finishing mill, comprising a first metal layer 1, a ceramic layer 2, an elastic layer 3 and a second metal layer 4;
[0024] The inner surface of the first metal layer 1 is bonded with a ceramic layer 2;
[0025] The inner surface of the ceramic layer 2 is fitted with a second metal layer 4;
[0026] Wherein, the second metal layer 4 is in clearance fit with the ceramic layer 2;
[0027] Wherein, an elastic layer 3 is arranged between the ceramic layer 2 and the second metal layer 4 .
[0028] Wherein, the first metal layer 1 contains (Cr, Fe) 7 C 3 Carbide; the second metal layer 4 is a stainless steel tube.
[0029] Wherein, the elastic layer 3 is silicone rubber; the elastic layer 3 is in interference fit with the gap formed by the ceramic layer 2 and the second metal layer 4 .
[0030] A method for preparing a high-temperature wear-resistant alloy guide roll of a finishing mill, comprising the following s...
Embodiment 2
[0038] A high-temperature wear-resistant alloy guide roll for a finishing mill, comprising a first metal layer 1, a ceramic layer 2, an elastic layer 3 and a second metal layer 4;
[0039] The inner surface of the first metal layer 1 is bonded with a ceramic layer 2;
[0040] The inner surface of the ceramic layer 2 is fitted with a second metal layer 4;
[0041] Wherein, the second metal layer 4 is in clearance fit with the ceramic layer 2;
[0042] Wherein, an elastic layer 3 is arranged between the ceramic layer 2 and the second metal layer 4 .
[0043] Wherein, the first metal layer 1 contains (Cr, Fe) 7 C 3 Carbide; the second metal layer 4 is a stainless steel tube.
[0044] Wherein, the elastic layer 3 is silicone rubber; the elastic layer 3 is in interference fit with the gap formed by the ceramic layer 2 and the second metal layer 4 .
[0045] A method for preparing a high-temperature wear-resistant alloy guide roll of a finishing mill, comprising the following s...
Embodiment 3
[0053]A high-temperature wear-resistant alloy guide roll for a finishing mill, comprising a first metal layer 1, a ceramic layer 2, an elastic layer 3 and a second metal layer 4;
[0054] The inner surface of the first metal layer 1 is bonded with a ceramic layer 2;
[0055] The inner surface of the ceramic layer 2 is fitted with a second metal layer 4;
[0056] Wherein, the second metal layer 4 is in clearance fit with the ceramic layer 2;
[0057] Wherein, an elastic layer 3 is arranged between the ceramic layer 2 and the second metal layer 4 .
[0058] Wherein, the first metal layer 1 contains (Cr, Fe) 7 C 3 Carbide; the second metal layer 4 is a stainless steel tube.
[0059] Wherein, the elastic layer 3 is silicone rubber; the elastic layer 3 is in interference fit with the gap formed by the ceramic layer 2 and the second metal layer 4 .
[0060] A method for preparing a high-temperature wear-resistant alloy guide roll of a finishing mill, comprising the following st...
PUM
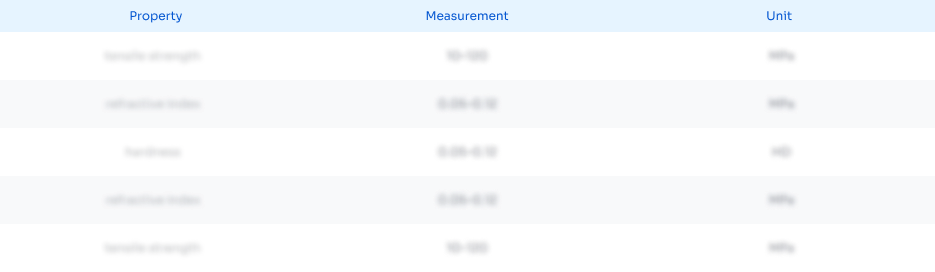
Abstract
Description
Claims
Application Information

- R&D
- Intellectual Property
- Life Sciences
- Materials
- Tech Scout
- Unparalleled Data Quality
- Higher Quality Content
- 60% Fewer Hallucinations
Browse by: Latest US Patents, China's latest patents, Technical Efficacy Thesaurus, Application Domain, Technology Topic, Popular Technical Reports.
© 2025 PatSnap. All rights reserved.Legal|Privacy policy|Modern Slavery Act Transparency Statement|Sitemap|About US| Contact US: help@patsnap.com