Lubricating oil composition for diesel engine and manufacturing method thereof
A technology for lubricating oil composition and diesel engine, applied in the directions of lubricating composition, petroleum industry, additives, etc., can solve the problems of shortening engine life, affecting engine operating condition performance, insufficient attention to rust prevention performance, etc.
- Summary
- Abstract
- Description
- Claims
- Application Information
AI Technical Summary
Problems solved by technology
Method used
Image
Examples
Embodiment 1
[0246] In a 500ml four-neck flask equipped with a stirrer, thermometer, condenser and dropping funnel, add 58.79g (0.323mol) of 2-tert-butyl-6-mercaptophenol, 6.88g (0.048mol) of boron trifluoride Ethyl ether (catalyst for alkylation reaction), 100ml of n-hexane solvent and 161.61g (0.162mol) of polyisobutene (Mn=1000, manufactured by Jihua Group Fine Chemicals Co., Ltd.) were reacted at 80°C for 2h. After the reaction, the reaction mixture was washed once with 5% potassium hydroxide solution by mass fraction, and washed to neutrality with hot water to remove the catalyst, and then the solvent and unreacted phenol were distilled off under reduced pressure to obtain polyisobutylene mercaptophenol, hydroxyl The value was 53.49 mgKOH / g. For the determination of hydroxyl value, refer to the acetic anhydride method in GB / T7383-2007.
[0247] An example reaction is as follows:
[0248]
[0249] From the proton nuclear magnetic spectrum analysis of the polyisobutylene mercaptoph...
Embodiment 2
[0251]
[0252] Under a nitrogen protection atmosphere, in a 250ml four-necked flask equipped with a stirrer, a thermometer, a condenser and a dropping funnel, add 30.58 grams (156 mmol) of 2-mercapto-4-methyl-6-methylphenol, 9.29 grams ( 112mmol) formaldehyde, 32.38g (176mmol) N-phenyl-p-phenylenediamine and 100mL toluene, stirred rapidly, and reacted at 100°C for 2h. After the reaction was finished, the solvent and a small amount of water generated were distilled off under reduced pressure, and the shielded phenol product with the structure shown in the title was obtained through column chromatography separation.
[0253] Product characterization data are as follows:
[0254] 1 H NMR (300MHz, CDCl 3 ): δ1.40(9H), 2.37(3H), 4.02(1H), 4.83(2H), 6.95-7.00(12H), 7.26(2H), 7.55(1H);
[0255] 13 C NMR (75MHz, CDCl 3 ): δ21.2, 30.1, 34.1, 49.9, 114.3, 118.9, 119.4, 121.8, 122.2, 125.8, 126.5, 129.5, 131.8, 132.3, 133.5, 143.3, 150.8;
[0256] C 24 h 28 N 2 OS calcd for ...
Embodiment 3
[0258]
[0259]Under nitrogen protection atmosphere, in the 250ml four-necked flask that stirrer, thermometer, condenser tube and dropping funnel are equipped with, add 31.65 grams (133mmol) 2,6-di-tert-butyl-4-mercaptophenol, 1.86 grams (62mmol ) formaldehyde, 28.15 grams (153 mmol) of N-phenyl-p-phenylenediamine, 0.75 grams (7.5 mmol) of hydrochloric acid and 150 mL of isopropanol, stirred rapidly, and reacted at 25 ° C for 24 h. After the reaction was finished, the solvent and a small amount of water generated were distilled off under reduced pressure, and the shielded phenol product with the structure shown in the title was obtained through column chromatography separation.
[0260] Product characterization data are as follows:
[0261] 1 H NMR (300MHz, CDCl 3 ): δ1.36-1.54(18H), 3.75(1H), 4.80(2H), 5.32(1H), 6.80(2H), 6.97(5H), 7.17(2H), 7.26(2H), 7.55(1H) ;
[0262] 13 C NMR (75MHz, CDCl 3 ): δ29.6, 34.6, 51.2, 119.4, 121.8, 126.5, 129.5, 131.4, 136.6, 144.5, 15...
PUM
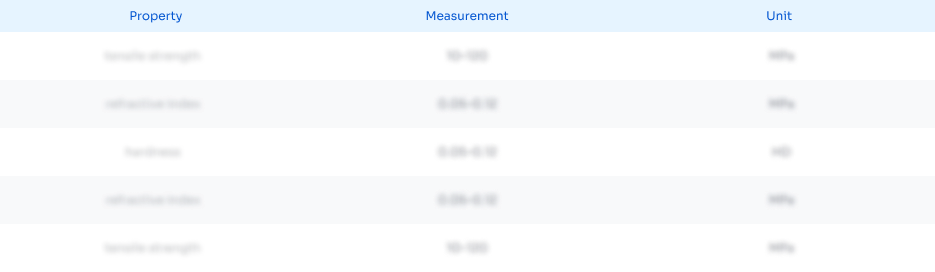
Abstract
Description
Claims
Application Information

- R&D Engineer
- R&D Manager
- IP Professional
- Industry Leading Data Capabilities
- Powerful AI technology
- Patent DNA Extraction
Browse by: Latest US Patents, China's latest patents, Technical Efficacy Thesaurus, Application Domain, Technology Topic, Popular Technical Reports.
© 2024 PatSnap. All rights reserved.Legal|Privacy policy|Modern Slavery Act Transparency Statement|Sitemap|About US| Contact US: help@patsnap.com