High strength ultraviolet resistant PE/ PET composite material and preparation method thereof
An anti-ultraviolet and composite material technology, applied in the field of polymer materials, can solve the problems of PE/PET composite material performance reduction, reduce the relative ratio of PE and PET, and use a large amount of compatibilizer to achieve high compatibility and improve mechanical properties. Great performance and filling capacity
- Summary
- Abstract
- Description
- Claims
- Application Information
AI Technical Summary
Problems solved by technology
Method used
Image
Examples
Embodiment 1
[0027] Take 100 parts of high-density polyethylene, 1.5 parts of maleic anhydride, 1.5 parts of glycidyl methacrylate, 0.4 parts of zinc stearate, take the corresponding parts of DCP according to Table 1, and mix them evenly in the high mixer, and put them in In the twin-screw extruder, the extrusion temperature is 200°C, the main engine speed is 590r / min, and the reaction time is 3-5min. After drawing, cooling and pelletizing. The results are shown in Table 1. The analysis of the results shows that when the DCP is increased to about 0.25 parts, the grafting rate and the melting finger reach the maximum at the same time. At this time, the grafting efficiency is high and the fluidity is good. Therefore, 0.2-0.3 parts of initiator is appropriate.
[0028] Table 1 The influence of DCP dosage on the grafting rate.
[0029]
Embodiment 2
[0031] Take 100 parts of high-density polyethylene, 0.25 parts of initiator, 0.4 parts of zinc stearate, and take the corresponding parts of maleic anhydride and glycidyl methacrylate according to Table 2 and mix them in a high-density mixer. In the screw extruder, the extrusion temperature is 200°C, the main engine speed is 590r / min, and the reaction time is 3-5min. After drawing, cooling, and pelletizing. The results are shown in Table 2. The result analysis shows that as the amount of MAH and GMA increases gradually, the melt index first decreases and then increases. When the melt index reaches the minimum value, the fluidity is poor and it is not easy to process. The comprehensive grafting efficiency is obtained. The amount of acetic anhydride and glycidyl methacrylate is preferably 1.2-1.5 parts.
[0032] Table 2 The influence of the amount of MAH and GMA on the grafting rate.
[0033]
Embodiment 3
[0035] Take 100 parts of high-density polyethylene, 1.5 parts of maleic anhydride, 1.5 parts of glycidyl methacrylate, 0.25 parts of initiator, and take corresponding parts of zinc stearate according to Table 3, mix them evenly in a high-mixer, and put them in In the twin-screw extruder, the extrusion temperature is 200°C, the main engine speed is 590r / min, and the reaction time is 3-5min. After drawing, cooling and pelletizing. The results are shown in Table 3. The result analysis shows that the content of lubricant zinc stearate has basically no effect on the melting finger. With the increase of the amount of zinc stearate, the color of the compatibilizer gradually becomes lighter until it is close to colorless. The smaller the effect of product color, and considering the cost of raw materials, the appropriate amount of zinc stearate is 0.3-0.5 parts.
[0036] Table 3 The influence of the amount of zinc stearate on the melt index.
[0037]
[0038] 2. The following examples furt...
PUM
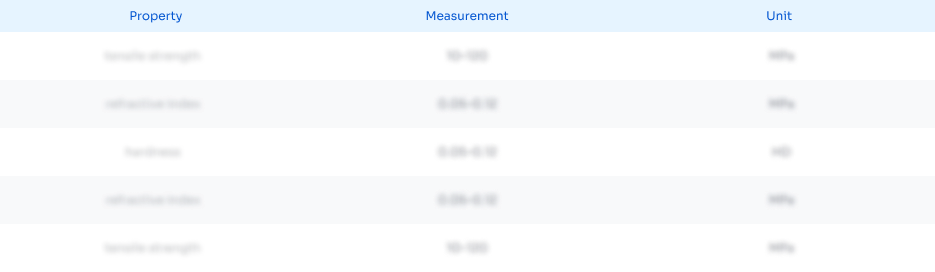
Abstract
Description
Claims
Application Information

- R&D
- Intellectual Property
- Life Sciences
- Materials
- Tech Scout
- Unparalleled Data Quality
- Higher Quality Content
- 60% Fewer Hallucinations
Browse by: Latest US Patents, China's latest patents, Technical Efficacy Thesaurus, Application Domain, Technology Topic, Popular Technical Reports.
© 2025 PatSnap. All rights reserved.Legal|Privacy policy|Modern Slavery Act Transparency Statement|Sitemap|About US| Contact US: help@patsnap.com