Process for the production of aromatic hydrocarbons and compositions obtained by the process
A technology for aromatic hydrocarbons and biomass raw materials, applied in the preparation of liquid hydrocarbon mixtures, hydrocarbon production from oxygen-containing organic compounds, organic chemistry, etc., can solve the problems of low carbon utilization, high raw material costs, and high hydrogen consumption
- Summary
- Abstract
- Description
- Claims
- Application Information
AI Technical Summary
Problems solved by technology
Method used
Examples
Embodiment 1
[0023] The raw material is 1 ton of bagasse, and the dry base cellulose content is 52%. After fully pulverizing the bagasse, stir and mix with 3.5 tons of 1.5% hydrochloric acid aqueous solution, then add 1.2 kg of ferric chloride, and keep the mixed solution at 1.0 MPa and 180°C for 10 minutes under microwave heating conditions to complete the acid reaction. The solution process, the liquid phase product can obtain 248 kilograms of levulinic acid and 95 kilograms of formic acid after separation.
[0024]Preparation of aromatization catalyst: Preparation of aromatization catalyst: Weigh 80 grams of ZSM-5 with a silicon-aluminum ratio of 50 and mix with 20 grams of pseudo-boehmite, add 3.9 grams of scallop powder, and mix well. Then add 45 grams of nitric acid aqueous solution with a mass percentage of nitric acid of 5.5%, knead and shape, and extrude. The obtained catalyst precursor was dried at 120° C. for 8 hours and calcined at 500° C. for 2 hours to obtain a molecular sie...
Embodiment 2
[0029] The raw material is 1 ton of pine sawdust, and the dry base cellulose content is 41.9%. After these pine chips are fully pulverized, they are stirred and mixed with 3.5 tons of 2.8% sulfuric acid aqueous solution. Under stirring conditions, the mixed solution is kept at 3.0 MPa and 205°C for 40 minutes to complete the acid hydrolysis process. 184 kg of levulinic acid and 75.6 kg of formic acid were obtained.
[0030] Preparation of aromatization catalyst: Weigh 60 grams of ZSM-11 with a silicon-to-aluminum ratio of 150 and mix it with 140 grams of kaolin, add 7.5 grams of astragalus powder, and mix well. Then add 5.5% of 92 grams of nitric acid aqueous solution, knead and shape, and extrude. The obtained catalyst precursor was dried at 120° C. for 8 hours and calcined at 500° C. for 2 hours to obtain a molecular sieve catalyst.
[0031] The levulinic acid containing stream is further converted over an aromatization catalyst. Reaction temperature 420°C, reaction press...
Embodiment 3
[0035] The raw material is 1 ton of municipal waste paper, and the dry base cellulose content is 92.1%. After these municipal waste papers are fully pulverized, they are stirred and mixed with 3.5 tons of 3.5% sulfuric acid aqueous solution, and then 13 kg of sodium sulfite is added, and the mixed solution is kept at 3.0 MPa and 205°C for 30 minutes under stirring conditions to complete the acidolysis process. After separation of the phase products, 503.5 kg of levulinic acid and 197.6 kg of formic acid were obtained.
[0036] Preparation of aromatization catalyst: Weigh 300 grams of MCM-22 with a silicon-aluminum ratio of 50 and mix them with 300 grams of pseudoboehmite, add 23 grams of celadon powder, and mix well. Then add 280 grams of nitric acid aqueous solution with a mass percent content of 5.5%, knead and shape, and extrude. The obtained catalyst precursor was dried at 120° C. for 8 hours and calcined at 550° C. for 2 hours to obtain a molecular sieve catalyst.
[00...
PUM
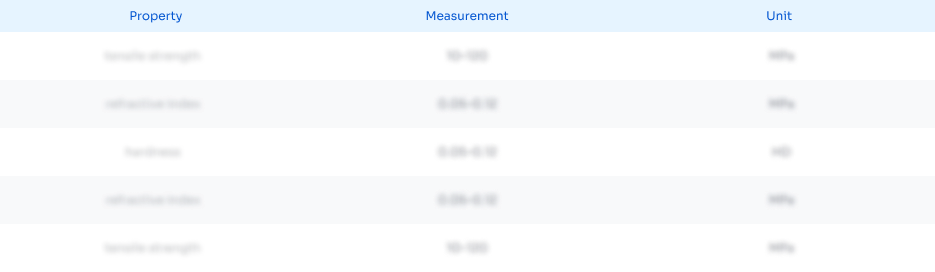
Abstract
Description
Claims
Application Information

- R&D
- Intellectual Property
- Life Sciences
- Materials
- Tech Scout
- Unparalleled Data Quality
- Higher Quality Content
- 60% Fewer Hallucinations
Browse by: Latest US Patents, China's latest patents, Technical Efficacy Thesaurus, Application Domain, Technology Topic, Popular Technical Reports.
© 2025 PatSnap. All rights reserved.Legal|Privacy policy|Modern Slavery Act Transparency Statement|Sitemap|About US| Contact US: help@patsnap.com